Rapid wax injection mold manufacturing process based on photo-curing 3D printing technique
A 3D printing and mold manufacturing technology, applied in the field of rapid mold manufacturing, can solve the problems of reducing the quality stability of batch castings, difficulty in ensuring consistency, and impact on the quality of metal parts, so as to save processing and manufacturing links, shorten the manufacturing cycle, Good dimensional stability
- Summary
- Abstract
- Description
- Claims
- Application Information
AI Technical Summary
Problems solved by technology
Method used
Image
Examples
Embodiment Construction
[0036] The present invention will be further described in detail below in conjunction with the accompanying drawings and examples. The following examples are explanations of the present invention and the present invention is not limited to the following examples.
[0037] Example.
[0038] see Figure 2-Figure 3 , which is a common open centrifugal pump impeller, generally adopts the traditional investment casting manufacturing process, but because the impeller has a complex curved surface shape, the manufacturing cost of the metal stamping wax mold is high, the cycle is long, and it is difficult to adapt to small batches Customized rapid production and manufacturing mode, and the process proposed by the present invention can better meet this demand.
[0039] see Figure 1 to Figure 5 , a rapid wax-pressing mold manufacturing process based on light-curing 3D printing technology, including the following process steps:
[0040] (1) CAD optimization design of mold structure
...
PUM
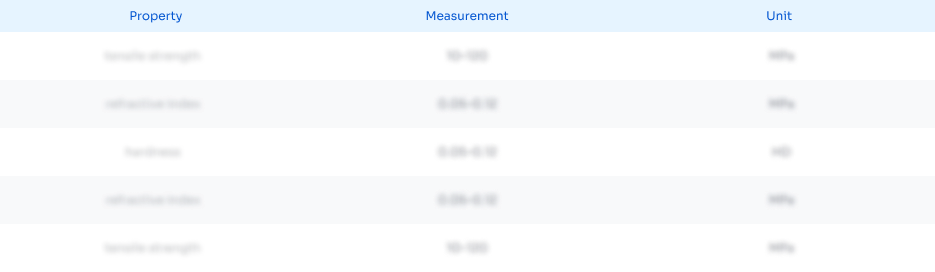
Abstract
Description
Claims
Application Information

- R&D Engineer
- R&D Manager
- IP Professional
- Industry Leading Data Capabilities
- Powerful AI technology
- Patent DNA Extraction
Browse by: Latest US Patents, China's latest patents, Technical Efficacy Thesaurus, Application Domain, Technology Topic, Popular Technical Reports.
© 2024 PatSnap. All rights reserved.Legal|Privacy policy|Modern Slavery Act Transparency Statement|Sitemap|About US| Contact US: help@patsnap.com