Rapid precise casting technology based on photocuring 3D printing technique
A 3D printing and precision casting technology, applied in the field of investment precision casting, can solve the problems of reducing the quality stability of batch castings, affecting the quality of metal parts, and difficulty in ensuring consistency, so as to improve product development efficiency, good surface quality, The effect of shortening the manufacturing cycle
- Summary
- Abstract
- Description
- Claims
- Application Information
AI Technical Summary
Problems solved by technology
Method used
Image
Examples
Embodiment Construction
[0027] The present invention will be further described in detail with reference to the accompanying drawings and embodiments. The following embodiments are for explaining the present invention and the present invention is not limited to the following embodiments.
[0028] Examples.
[0029] See figure 1 , A rapid precision casting process based on light curing 3D printing technology, including the following steps:
[0030] (1) CAD optimization design of 3D model
[0031] Based on 3D modeling software such as Pro / E, UG, SolidWorks, etc., optimize the CAD casting process design for the target part model.
[0032] See Figure 2-Figure 3 , Establish a three-dimensional model 1 of the target part, and design the corresponding gating system 2 directly on the part model. The gating system 2 includes structures such as a sprue cup, a straight gate, a horizontal gate and an inner gate, so that the target part is a three-dimensional model 1 and its gating system 2 form an overall model of the t...
PUM
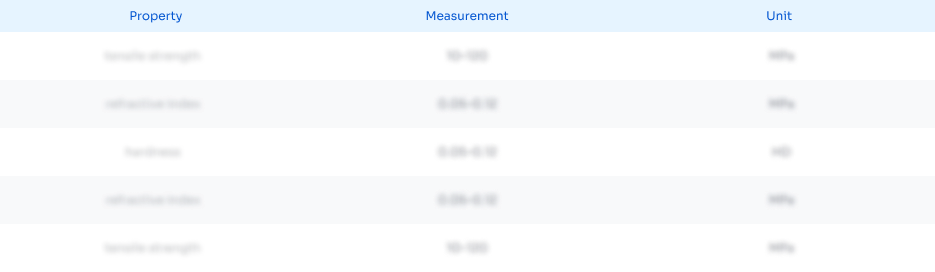
Abstract
Description
Claims
Application Information

- R&D
- Intellectual Property
- Life Sciences
- Materials
- Tech Scout
- Unparalleled Data Quality
- Higher Quality Content
- 60% Fewer Hallucinations
Browse by: Latest US Patents, China's latest patents, Technical Efficacy Thesaurus, Application Domain, Technology Topic, Popular Technical Reports.
© 2025 PatSnap. All rights reserved.Legal|Privacy policy|Modern Slavery Act Transparency Statement|Sitemap|About US| Contact US: help@patsnap.com