Special demoulding agent for concrete and preparation method thereof
A release agent and concrete technology, which is applied in manufacturing tools, petroleum industry, ceramic molding machines, etc., can solve problems such as the contradiction between release performance and stability, and achieve the effect of improving appearance and excellent release performance.
- Summary
- Abstract
- Description
- Claims
- Application Information
AI Technical Summary
Problems solved by technology
Method used
Image
Examples
Embodiment 1
[0031] Take 480g of water, 0.4g of sodium hydroxide, 16.7g of the mixture of SE-10N and Tween 60 and add them into the reaction kettle 1, and stir at room temperature for 30min at a rotation speed of 3000rpm.
[0032] Glyceryl trioleate 200g, methacryloxypropyltrimethoxysilane 20g, No. 5# liquid paraffin 10g, initiator NaPS 0.1g, SE-10N and Tween 60 mixture 33.4g and water 240g were added to In the reaction kettle 2, the pre-emulsion was obtained by stirring at room temperature for 30 minutes under the condition of 3000 rpm.
[0033] The prepared pre-emulsion was added dropwise into Reactor 1 for 30 minutes and reacted for 2 hours. Continue to heat up the emulsion to 60°C. After reacting for 2 hours, continue to add 0.5 g of mineral oil defoamer, stop heating, and wait for natural cooling to obtain the special release agent for concrete.
[0034] Dilute to about 10% solid content for use. After the JC / T945-2005 standard test, the demoulding effect is good, and the concrete a...
Embodiment 2
[0036] Take 385g of water, 0.6g of sodium hydroxide, SR-10 and 23g of the mixture of fatty alcohol and ethylene oxide condensate MOA-3 into the reaction kettle 1, and stir at room temperature for 30min at a speed of 3000rpm. 250g of butyl oleate, 50g of methacryloxypropyltriethoxysilane, 50g of 15# liquid paraffin, 0.2g of initiator NaPS, SR-10 and MOA- 3. Add 46 g of the mixture and 192.5 g of water into Reactor 2 and stir at room temperature for 30 min at 3000 rpm to obtain a pre-emulsion.
[0037] The prepared pre-emulsion was added dropwise into Reactor 1 for 45 minutes and reacted for 2 hours. Continue to heat up the emulsion to 60°C. After reacting for 3 hours, continue to add 0.6 g of mineral oil defoamer, stop heating, and wait for natural cooling to obtain the special release agent for concrete.
[0038] Dilute to about 10% solid content for use. After the JC / T945-2005 standard test, the demoulding effect is good, and the concrete adhesion after demoulding is 1.7g / m...
Embodiment 3
[0040] Take 299g of water, 0.8g of sodium hydroxide, 33.3g of a mixture of COPS-2 and castor oil polyoxyethylene ether EL-60, and add it to Reactor 1, and stir at room temperature for 30min at a speed of 3000rpm.
[0041] Mix amyl oleate 300g, methacryloxypropyl triisopropoxysilane 80g, No. 26# liquid paraffin 70g, initiator NaPS 0.3g, COPS-2 and castor oil polyoxyethylene ether EL-60 66.6g and 149.5g of water were added into Reactor 2 and stirred at room temperature for 30min at 3000rpm to obtain a pre-emulsion.
[0042] Add the prepared pre-emulsion dropwise into the reaction kettle 1, the dropwise addition time is 1h, and react for 2h. Continue to heat up the emulsion to 70°C. After reacting for 4 hours, continue to add 0.8 g of mineral oil defoamer, stop heating, and wait for natural cooling to obtain the special release agent for concrete.
[0043]Dilute to about 10% solid content for use. After the JC / T945-2005 standard test, the demoulding effect is good, and the conc...
PUM
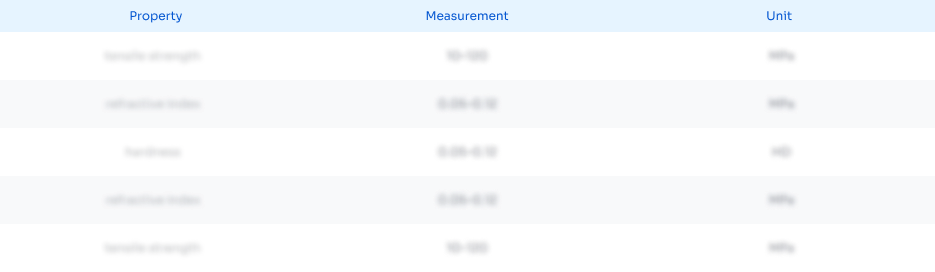
Abstract
Description
Claims
Application Information

- Generate Ideas
- Intellectual Property
- Life Sciences
- Materials
- Tech Scout
- Unparalleled Data Quality
- Higher Quality Content
- 60% Fewer Hallucinations
Browse by: Latest US Patents, China's latest patents, Technical Efficacy Thesaurus, Application Domain, Technology Topic, Popular Technical Reports.
© 2025 PatSnap. All rights reserved.Legal|Privacy policy|Modern Slavery Act Transparency Statement|Sitemap|About US| Contact US: help@patsnap.com