Highly heat-resistant graphite film metal composite and preparation method thereof
A metal composite material and composite material technology, applied in the field of high heat-resistant graphite film metal composite material and its preparation, can solve the problems of being unable to meet the requirements of the use environment, low cost, poor solvent resistance, and low heat resistance. Achieve good electromagnetic shielding properties, good resistance to conventional solvents and high temperature resistance, and excellent thermal conductivity
- Summary
- Abstract
- Description
- Claims
- Application Information
AI Technical Summary
Problems solved by technology
Method used
Image
Examples
Embodiment 1
[0038] Add 15 parts of self-made thermoplastic polyimide powder to 80 parts of DMF solvent, stir at room temperature until completely dissolved; then add 5 parts of treated ultrafine artificial graphite powder, and stir at 40°C for 2 hours to obtain Thermoplastic polyimide adhesive; apply the obtained thermoplastic polyimide adhesive on the roughened surface of copper foil with an automatic film coating machine, dry it at 140°C for 5min, and then apply it at 160°C Its rubber surface is pressed with the graphite film to obtain the graphite film copper foil composite material, which is recorded as Example 1.
Embodiment 2
[0040] Add 25 parts of self-made thermoplastic polyimide powder to 70 parts of DMF solvent, stir at room temperature until completely dissolved; then add 4.5 parts of treated ultra-fine artificial graphite powder and 0.5 part of aluminum nitride, in Stir at 50°C for 2 hours to obtain a thermoplastic polyimide adhesive; apply the obtained thermoplastic polyimide adhesive to the roughened surface of copper foil with an automatic film coating machine, and dry it at 140°C for 5 minutes , and then at 160° C., press the rubberized surface with the graphite film to obtain the graphite film-copper foil composite material, which is referred to as Example 2.
Embodiment 3
[0042] Add 20 parts of self-made thermoplastic polyimide powder to 75 parts of DMF solvent, stir at room temperature until completely dissolved; then add 3 parts of treated ultrafine artificial graphite powder, 1 part of carbon nanotube and 1 part of Aluminum nitride was added to it, and stirred at 30°C for 3 hours to obtain a thermoplastic polyimide adhesive; the obtained thermoplastic polyimide adhesive was coated on the roughened surface of the copper foil with an automatic film coating machine, and the Drying treatment at 150°C for 4 minutes, and then pressing the glued surface with the graphite film at 170°C to obtain a graphite-film-copper-foil composite material, which is referred to as Example 3.
PUM
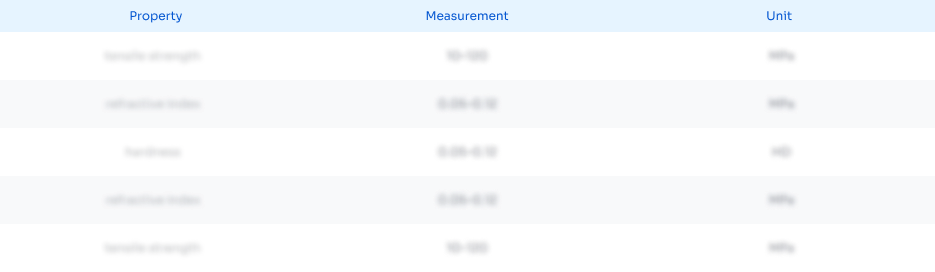
Abstract
Description
Claims
Application Information

- R&D
- Intellectual Property
- Life Sciences
- Materials
- Tech Scout
- Unparalleled Data Quality
- Higher Quality Content
- 60% Fewer Hallucinations
Browse by: Latest US Patents, China's latest patents, Technical Efficacy Thesaurus, Application Domain, Technology Topic, Popular Technical Reports.
© 2025 PatSnap. All rights reserved.Legal|Privacy policy|Modern Slavery Act Transparency Statement|Sitemap|About US| Contact US: help@patsnap.com