Activated sintering method of aluminum or aluminum alloy
A technology of activated sintering and aluminum alloy, which is applied in metal processing equipment, transportation and packaging, etc. It can solve the problems of residual sintering, poor surface layer, high equipment requirements, etc., and achieve the effect of improving sinterability, simple process and enhancing material transfer
- Summary
- Abstract
- Description
- Claims
- Application Information
AI Technical Summary
Problems solved by technology
Method used
Image
Examples
Embodiment 1
[0030] In this embodiment, pure aluminum is taken as an example to illustrate the activation sintering method of aluminum or aluminum alloy, which specifically includes the following steps:
[0031] (1) Preparation of mixed salt powder
[0032] With deionized water as solvent, under the action of heating and magnetic stirring, LiCl, KCl, K 2 ZrF 6 Mixed salt solutions with mass fractions of 20%, 4%, and 1.5% were stirred evenly and fully dried at 60°C to obtain mixed salt powder;
[0033] (2) Surface modification of aluminum powder
[0034] Disperse a certain quality of the above mixed salt powder in absolute ethanol, and the weight ratio of the mixed salt powder to absolute ethanol is 1:40, fully dissolve the added mixed salt powder under magnetic stirring, and then add a certain quality of aluminum powder, so that the mass ratio of the mixed salt mass to the aluminum powder is 0.01, continue to stir for 90 minutes, and then fully dry at 50°C to obtain a surface-modified r...
Embodiment 2
[0040] This embodiment takes 2014 aluminum alloy parts as an example to illustrate the activation sintering method of aluminum or aluminum alloy, which specifically includes the following steps:
[0041] (1) Preparation of mixed salt solution
[0042] With deionized water as solvent, under the action of heating and magnetic stirring, LiCl, KCl, K 2 ZrF 6 For mixed solutions with mass fractions of 12%, 2%, and 1%, respectively, after the three powders are fully dissolved, continue heating and stirring for 5 minutes and then stop;
[0043] (2) Surface modification of 2014 aluminum alloy powder
[0044] Add a certain mass of 2014 aluminum alloy powder to the above mixed salt solution, the mass ratio of the above mixed salt to it is 0.001, fully disperse the added powder under magnetic stirring, continue stirring for 60 minutes, and then fully dry at 60°C to obtain surface modification 2014 aluminum alloy powder;
[0045] (3) Forming
[0046] Using a V-shaped mixer, mix 0.5wt...
Embodiment 3
[0050] In this embodiment, taking 6061 aluminum alloy as an example, the activated sintering method of aluminum or aluminum alloy is described, which specifically includes the following steps:
[0051] (1) Preparation of mixed salt solution
[0052] With deionized water as solvent, under the action of heating and magnetic stirring, LiCl, KCl, K 2 ZrF 6 Mixed solutions with mass fractions of 18%, 5%, and 0.1%, respectively, after the three powders are fully dissolved, continue heating and stirring for 8 minutes and then stop;
[0053] (2) Surface modification of 6061 aluminum alloy powder
[0054] Add a certain mass of 6061 aluminum alloy powder to the above mixed salt solution, the mass ratio of the above mixed salt to it is 0.008, fully disperse the added powder under magnetic stirring, continue stirring for 60 minutes, and then fully dry at 50°C to obtain surface modification 6061 aluminum alloy powder;
[0055] (3) Forming
PUM
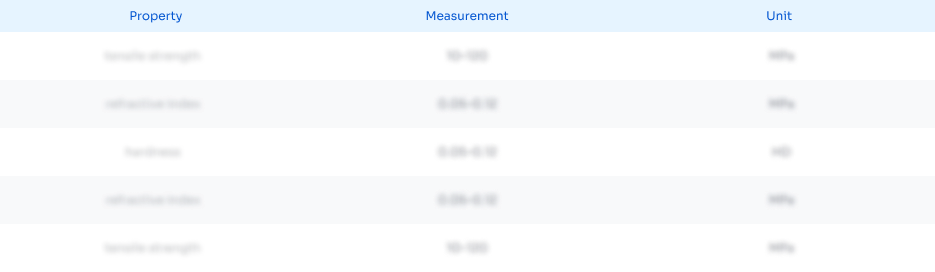
Abstract
Description
Claims
Application Information

- R&D
- Intellectual Property
- Life Sciences
- Materials
- Tech Scout
- Unparalleled Data Quality
- Higher Quality Content
- 60% Fewer Hallucinations
Browse by: Latest US Patents, China's latest patents, Technical Efficacy Thesaurus, Application Domain, Technology Topic, Popular Technical Reports.
© 2025 PatSnap. All rights reserved.Legal|Privacy policy|Modern Slavery Act Transparency Statement|Sitemap|About US| Contact US: help@patsnap.com