Surface treatment process for enhancing electrolytic copper foil anti-oxidization performance
A technology of electrolytic copper foil and surface treatment, which is applied in the field of surface treatment of electrolytic copper foil to achieve good application prospects and improve the effect of high temperature oxidation resistance
- Summary
- Abstract
- Description
- Claims
- Application Information
AI Technical Summary
Problems solved by technology
Method used
Image
Examples
Embodiment 1
[0015] A surface treatment process for improving the high-temperature anti-oxidation performance of electrolytic copper foil, comprising the following steps: 1) dissolving complexing agents potassium sodium tartrate, zinc sulfate, additive A and additive B in water respectively, and keeping it clear after mixing to obtain an electroplating solution, Additive A is a mixture of ammonium molybdate, aluminum sulfate, zirconium sulfate and indium sulfate in a mass ratio of 4:2:1:1, additive B is a mixture of sodium thiosulfate and sodium hypophosphite in a mass ratio of 2:1 The resulting mixture, the content of potassium sodium tartrate in the electroplating solution is 50g / L, the content of zinc sulfate is 20g / L, the content of additive A is 6g / L, and the content of additive B is 3g / L; 1. The electrolytic copper foil obtained after solidification is placed in the electroplating solution obtained in step 1) for electroplating. The temperature of the electroplating solution is 45±2°C...
Embodiment 2
[0016] A surface treatment process for improving the high-temperature anti-oxidation performance of electrolytic copper foil, comprising the following steps: 1) dissolving complexing agents potassium sodium tartrate, zinc sulfate, additive A and additive B in water respectively, and keeping it clear after mixing to obtain an electroplating solution, Additive A is a mixture of ammonium molybdate, silver sulfate, zirconium sulfate and sodium vanadate at a mass ratio of 4:2:1:1, and additive B is a mixture of sodium sulfite and potassium dihydrogen phosphate at a mass ratio of 2:1 The mixture, the content of potassium sodium tartrate in the electroplating solution is 60g / L, the content of zinc sulfate is 30g / L, the content of additive A is 10g / L, and the content of additive B is 5g / L; The electrolytic copper foil obtained after melting and curing is placed in the electroplating solution obtained in step 1) for electroplating. The temperature of the electroplating solution is 35±2°...
Embodiment 3
[0018] A surface treatment process for improving the high-temperature anti-oxidation performance of electrolytic copper foil, comprising the following steps: 1) dissolving complexing agents potassium sodium tartrate, zinc sulfate, additive A and additive B in water respectively, and keeping it clear after mixing to obtain an electroplating solution, Additive A is a mixture of sodium tungstate, silver sulfate, aluminum sulfate and sodium vanadate in a mass ratio of 4:2:1:1, additive B is a mixture of sodium thiosulfate and sodium phosphite in a mass ratio of 2:1 The resulting mixture, the content of potassium sodium tartrate in the electroplating solution is 30g / L, the content of zinc sulfate is 10g / L, the content of additive A is 1g / L, and the content of additive B is 0.5g / L; The electrolytic copper foil obtained after washing, roughening, and solidification is placed in the electroplating solution obtained in step 1) for electroplating. Nanoscale zinc alloy coating; 3) The el...
PUM
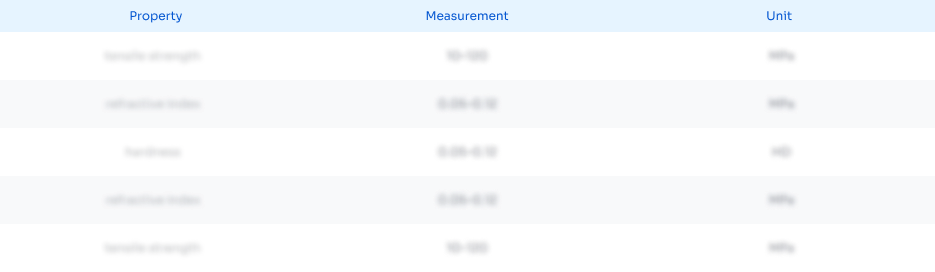
Abstract
Description
Claims
Application Information

- R&D Engineer
- R&D Manager
- IP Professional
- Industry Leading Data Capabilities
- Powerful AI technology
- Patent DNA Extraction
Browse by: Latest US Patents, China's latest patents, Technical Efficacy Thesaurus, Application Domain, Technology Topic, Popular Technical Reports.
© 2024 PatSnap. All rights reserved.Legal|Privacy policy|Modern Slavery Act Transparency Statement|Sitemap|About US| Contact US: help@patsnap.com