Environment-friendly metallurgy extracting method for lead-zinc oxide ores
A technology for oxidizing lead and zinc and oxidizing ore, which is applied in the improvement of process efficiency, photographic technology, instruments, etc., can solve the problems of difficult discharge, increase the treatment of lead system wastewater, and difficulty in solution circulation, and achieve strong adaptability and lightening. burden, avoid large cumulative effects
- Summary
- Abstract
- Description
- Claims
- Application Information
AI Technical Summary
Problems solved by technology
Method used
Image
Examples
Embodiment 1
[0051] First, lead-zinc oxide and coal are mixed at a coal ratio of 45% and sent to a rotary kiln for reduction and volatilization. The temperature is 1300°C and the volatilization time is 90 minutes; , cement, paving materials. Volatile smoke is collected to obtain oxide powder, which contains 62% Zn and 13.5% Pb. Neutral leaching with acidic leaching solution, H 2 SO 4 70g / L, liquid-solid ratio 3:1, temperature 75-80°C, leaching time 60-70min, leaching end pH 5.0-5.5. After the neutral leaching, the solution is routinely purified, the cathode zinc is deposited after electrowinning, and the zinc ingot (purity 99.99-99.995%) is obtained by melting and casting. The neutral leaching slag is acid leached with zinc electrolytic waste liquid and lead electrolytic waste liquid. Fe in solution 总 2 SO 4 The concentration is 120g / L; the lead sulfate slurry is continuously added to the suspension electrolyzer at a certain speed, and the cathode current density is 250A / m 2 , lead...
Embodiment 2
[0053] First, lead-zinc oxide and coal are mixed at a coal ratio of 55% and sent to a rotary kiln for reduction and volatilization. The temperature is 1200°C and the volatilization time is 120 minutes; , cement, paving materials. Volatile fumes are collected to obtain oxide powder, which contains 63.5% Zn and 14.5% Pb. Neutral leaching with acidic leaching solution, H 2 SO 4 50g / L, liquid-solid ratio 3:1, temperature 75-80°C, leaching time 80-90min, leaching end pH 5.0-5.5. After the neutral leaching, the solution is routinely purified, the cathode zinc is deposited after electrowinning, and the zinc ingot (purity 99.99-99.995%) is obtained by melting and casting. The neutral leaching slag is acid leached with zinc electrolytic waste liquid and lead electrolytic waste liquid. The initial acid of leaching is 150g / L, the liquid-solid ratio is 3:1, the temperature is 85-90°C, and the time is 90min. Fe in solution 总 2 SO 4 The concentration is 150g / L; the lead sulfate slurry ...
Embodiment 3
[0055] First, lead-zinc oxide and coal are mixed with 60% coal and sent to the rotary kiln for reduction and volatilization. The temperature is 1250°C and the volatilization time is 110 minutes; , cement, paving materials. Volatile fumes are collected to obtain oxide powder, which contains 65.5% Zn and 13.5% Pb. Neutral leaching with acidic leaching solution, H 2 SO 4 30g / L, liquid-solid ratio 3:1, temperature 75-80°C, leaching time 80-90min, leaching end pH 5.0-5.5. After the neutral leaching, the solution is routinely purified, the cathode zinc is deposited after electrowinning, and the zinc ingot (purity 99.99-99.995%) is obtained by melting and casting. The neutral leaching slag is acid leached with zinc electrolytic waste liquid and lead electrolytic waste liquid. The initial acid of leaching is 200g / L, the liquid-solid ratio is 3:1, the temperature is 90-95°C, and the time is 80min. The acidic leaching liquid is neutralized to remove iron and iron. Fe in solution 总...
PUM
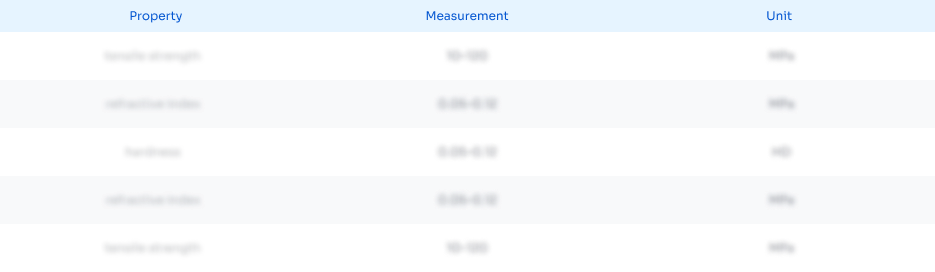
Abstract
Description
Claims
Application Information

- R&D
- Intellectual Property
- Life Sciences
- Materials
- Tech Scout
- Unparalleled Data Quality
- Higher Quality Content
- 60% Fewer Hallucinations
Browse by: Latest US Patents, China's latest patents, Technical Efficacy Thesaurus, Application Domain, Technology Topic, Popular Technical Reports.
© 2025 PatSnap. All rights reserved.Legal|Privacy policy|Modern Slavery Act Transparency Statement|Sitemap|About US| Contact US: help@patsnap.com