Lubricating grease for underwater spindle noses of iron-making auger conveyors and preparation method
The technology of a grease and a composition is applied in the field of grease and preparation for the underwater shaft head of an iron-making cage stirring machine, and achieves the effect of improving the anti-rust performance of salt spray, good anti-rust ability and good anti-rust performance of salt spray
- Summary
- Abstract
- Description
- Claims
- Application Information
AI Technical Summary
Problems solved by technology
Method used
Image
Examples
Embodiment Construction
[0024] The present invention will be further elaborated below by specific examples.
[0025] Each embodiment and comparative example preparation method:
[0026] Embodiment 1-8 and comparative example
[0027] Thickener lithium 12 hydroxystearate, calcium 12 hydroxystearate, complex soap with a mass ratio of lithium suberate 3:1:1 and 45%-55% base oil are added to the reaction kettle, stirred and heated To 220-230°C, keep the temperature constant for 25 minutes, add 10%-20% base oil to cool, continue to stir, add the remaining base oil, stir to cool down to below 70°C, add additives, stir and mix evenly. The composition is oil-pressed three times by a three-roller machine, and then packed in a finished product.
[0028] Embodiment 1-8 component content and comparative example component content are shown in Table 1
[0029] Table 1 embodiment 1-8 component content and comparative example component content
[0030]
[0031] Embodiment 1-8 and comparative example performan...
PUM
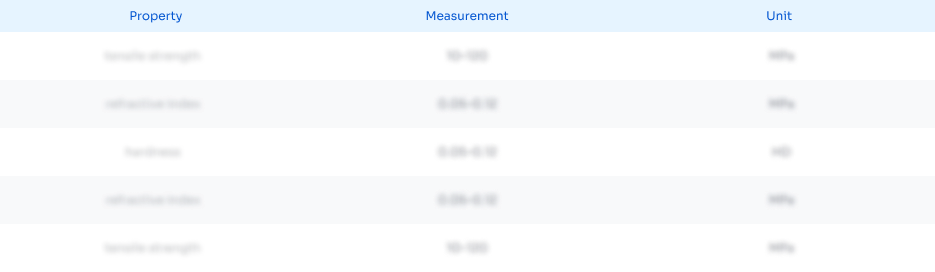
Abstract
Description
Claims
Application Information

- R&D Engineer
- R&D Manager
- IP Professional
- Industry Leading Data Capabilities
- Powerful AI technology
- Patent DNA Extraction
Browse by: Latest US Patents, China's latest patents, Technical Efficacy Thesaurus, Application Domain, Technology Topic, Popular Technical Reports.
© 2024 PatSnap. All rights reserved.Legal|Privacy policy|Modern Slavery Act Transparency Statement|Sitemap|About US| Contact US: help@patsnap.com