Ceramic brake pad
A technology of brake pads and ceramics, which is applied in the field of ceramic brake pads, can solve the problems of easily damaged friction discs, decreased wear resistance, and reduced strength and rigidity, and achieves the effects of no damage to friction discs, long service life, and high cost performance
- Summary
- Abstract
- Description
- Claims
- Application Information
AI Technical Summary
Problems solved by technology
Method used
Examples
Embodiment 1
[0011] A ceramic brake pad, which is composed of the following components: nitrile rubber powder 1-5kg, sound-absorbing powder 5-10kg, resin 6-10kg, whiskers 3-8kg, brass fiber 3-8kg, short fiber 1-4kg, Friction powder 1~5kg, long fiber 1~4kg, ceramic fiber 8~16kg, high temperature barium 3~8kg, flake graphite (-195) 4~9kg, iron 0.5~3kg, petroleum coke 2~6kg, ceramic additive 8~ 13kg, wear-resistant powder 8-13kg, aramid fiber 0.5-3kg, wood fiber 1-4kg, ceramic grinding agent 2-6kg, antimony sulfide 1-4kg, stabilizer 3-8kg.
[0012] When making, weigh according to the above formula requirements, grind the material into fine particles, and then send it to the mixer for mixing; use the hot pressing mold for the prepared steel back and ingredients at a temperature of 160°C, a pressure of 115MPa, and a time of Hot press forming under the condition of 10min, put the above hot press formed product into a temperature-controlled drying furnace for heat treatment; finally, it can be us...
Embodiment 2
[0014] A ceramic brake pad consisting of the following components: nitrile rubber powder 3kg, silencing powder 7kg, resin 8kg, whisker 6kg, brass fiber 5kg, short fiber 2kg, friction powder 3 kg, long fiber 2kg, ceramic fiber 11kg , high temperature barium 5kg, flake graphite (-195) 6kg, iron 1.5kg, petroleum coke 4kg, ceramic additive 10kg, wear-resistant powder 10kg, aramid fiber 1.5kg, wood fiber 2kg, ceramic grinding agent 4kg, antimony sulfide 2kg, Stabilizer 5kg.
[0015] When making, weigh according to the above formula requirements, grind the material into fine particles, and then send it to the mixer for mixing; use the hot pressing mold for the prepared steel back and ingredients at a temperature of 160°C, a pressure of 115MPa, and a time of Hot press forming under the condition of 10min, put the above hot press formed product into a temperature-controlled drying furnace for heat treatment; finally, it can be used after spraying and trimming.
PUM
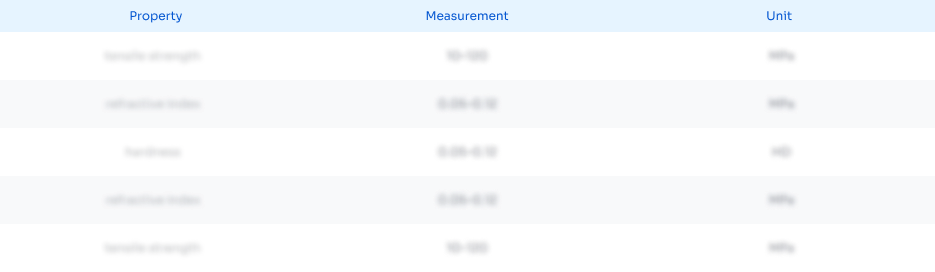
Abstract
Description
Claims
Application Information

- Generate Ideas
- Intellectual Property
- Life Sciences
- Materials
- Tech Scout
- Unparalleled Data Quality
- Higher Quality Content
- 60% Fewer Hallucinations
Browse by: Latest US Patents, China's latest patents, Technical Efficacy Thesaurus, Application Domain, Technology Topic, Popular Technical Reports.
© 2025 PatSnap. All rights reserved.Legal|Privacy policy|Modern Slavery Act Transparency Statement|Sitemap|About US| Contact US: help@patsnap.com