Preparation method for thermosetting hard resin
A solid resin and thermosetting technology, which is applied in the field of thermosetting resin preparation, can solve the problems of high risk of resin gel, high resin viscosity, and difficult control, and achieve stable friction coefficient, avoid resin gelation, and wear resistance Good results
- Summary
- Abstract
- Description
- Claims
- Application Information
AI Technical Summary
Problems solved by technology
Method used
Image
Examples
Embodiment 1
[0014] Phenol 500g, 37% formaldehyde solution 776g and ammonia water (25%) 12.5g are dropped in the reaction vessel that has thermometer, agitator, reflux condenser, heat up to 70 DEG C constant temperature reaction 1 hour, heat up to 85 DEG C and react 90 Minutes, then distilled under reduced pressure at a vacuum degree of -0.092MPa, the dehydration temperature does not exceed 65°C, when the moisture content in the resin reaches 1.56wt%, pour the resin into an enamel dish, put it in an oven at 70°C, and when the resin is polymerized When the speed reaches 54S, the enamel dish is taken out from the oven and cooled to obtain 641g of thermosetting resin.
Embodiment 2
[0016] Put 500g of phenol, 776g of 37% formaldehyde solution and 10g of sodium hydroxide solution (47%) into a reaction vessel with a thermometer, a stirring device, and a reflux condenser, heat up to 70°C for constant temperature reaction for 1 hour, then heat up to 85°C React for 90 minutes, then distill under reduced pressure under vacuum degree -0.092MPa pressure, dehydration temperature does not exceed 65°C, when the moisture content in the resin reaches 1.56wt%, pour the resin into an enamel plate, put it in an oven at 70°C, and when The polymerization rate of the resin reached 56S, and the enamel dish was taken out from the oven to cool down to obtain 651g of resin.
Embodiment 3
[0018] Phenol 500g, cashew nut oil 50g, 37% formaldehyde aqueous solution 806g and ammoniacal liquor (25%) 12.5g drop in the reaction container that has thermometer, stirring device, reflux condenser, heat up to 70 ℃ of constant temperature reaction 1 hour, be warmed up to React at 85°C for 90 minutes, then distill under reduced pressure at a vacuum degree of -0.092MPa, and the dehydration temperature does not exceed 65°C. When the moisture content in the resin reaches 1.96wt%, pour the resin into an enamel tray and put it in an oven at 70°C. When the polymerization speed of the resin reaches 57S, the enamel plate is taken out from the oven and cooled to obtain 712 resin.
PUM
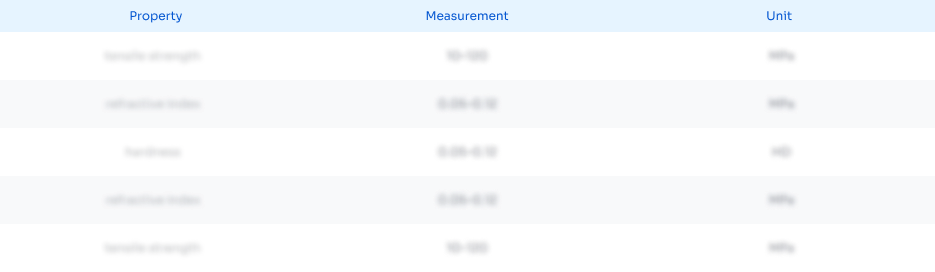
Abstract
Description
Claims
Application Information

- Generate Ideas
- Intellectual Property
- Life Sciences
- Materials
- Tech Scout
- Unparalleled Data Quality
- Higher Quality Content
- 60% Fewer Hallucinations
Browse by: Latest US Patents, China's latest patents, Technical Efficacy Thesaurus, Application Domain, Technology Topic, Popular Technical Reports.
© 2025 PatSnap. All rights reserved.Legal|Privacy policy|Modern Slavery Act Transparency Statement|Sitemap|About US| Contact US: help@patsnap.com