Super-wide linen fabric and production process thereof
A production process, linen technology, applied in the direction of fabric surface trimming, weaving, and improved hand feeling fibers, etc., can solve the problems of unstable shrinkage, failure to meet customer needs, and decline in strength, so as to achieve soft texture and improved evenness , Improve the effect of easy wrinkles
- Summary
- Abstract
- Description
- Claims
- Application Information
AI Technical Summary
Problems solved by technology
Method used
Examples
Embodiment 1
[0027] A production process of an extra-wide linen fabric, comprising the steps of:
[0028] Step 1, using a silicone softening agent to soften the flax roving, wherein the amount of the silicone softening agent is 4% of the quality of the flax roving, the pH value of the treatment is 5, and the temperature is kept at 45° C. for 24 minutes;
[0029] Step 2, performing high-frequency drying treatment on the oversoft flax raw yarn, so that the moisture content of the raw yarn is 5%;
[0030] Step 3: Winding and waxing the raw flax yarn after high-frequency drying to keep the moisture content of the raw yarn at 15%;
[0031] Step 4, steaming the wax-sealed flax, the steaming temperature is 65°C, the heating time is 1 hour, and the heat preservation is 10 minutes;
[0032] Step 5: Weaving the steamed linen raw yarn on the machine to obtain the gray cloth; the weaving is on a 34-inch 30G double-sided jacquard machine, according to the 84-way needle arrangement, edit and design the...
Embodiment 2
[0038] A production process of an extra-wide linen fabric, comprising the steps of:
[0039] Step 1, using a silicone softening agent to soften the flax roving, wherein the amount of the silicone softening agent is 5% of the mass of the flax roving, the pH value of the treatment is 6, and the temperature is kept at 45° C. for 24 minutes;
[0040] Step 2, performing high-frequency drying treatment on the oversoft flax raw yarn, so that the moisture content of the raw yarn is 10%;
[0041] Step 3: Winding and waxing the raw flax yarn after high-frequency drying to keep the moisture content of the raw yarn at 20%;
[0042] Step 4, steaming the wax-sealed flax, the steaming temperature is 65°C, the heating time is 1 hour, and the heat preservation is 10 minutes;
[0043]Step 5: Weaving the steamed linen raw yarn on the machine to obtain the gray cloth; the weaving is on a 34-inch 30G double-sided jacquard machine, according to the 84-way needle arrangement, edit and design the pa...
PUM
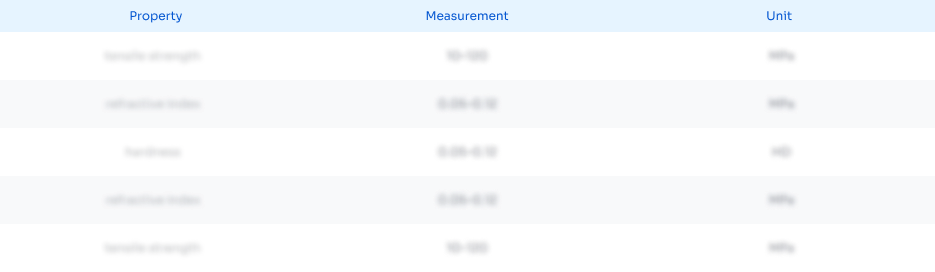
Abstract
Description
Claims
Application Information

- R&D
- Intellectual Property
- Life Sciences
- Materials
- Tech Scout
- Unparalleled Data Quality
- Higher Quality Content
- 60% Fewer Hallucinations
Browse by: Latest US Patents, China's latest patents, Technical Efficacy Thesaurus, Application Domain, Technology Topic, Popular Technical Reports.
© 2025 PatSnap. All rights reserved.Legal|Privacy policy|Modern Slavery Act Transparency Statement|Sitemap|About US| Contact US: help@patsnap.com