Self-unloading twin granary with more uniform grain distribution
A dual-body, self-unloading technology, used in loading/unloading, fruit suspension devices, conveyors, etc., can solve the problems of small grain porosity, poor effect, mold growth, etc., so as to reduce the overall occupied space and save driving. The effect of motor and grain distribution evenly
- Summary
- Abstract
- Description
- Claims
- Application Information
AI Technical Summary
Problems solved by technology
Method used
Image
Examples
Embodiment 1)
[0041] Figure 1 to Figure 25 A first embodiment of the invention is shown.
[0042] This embodiment is a relatively uniform self-unloading double-body granary for grain distribution, see Figure 1 to Figure 8 Shown, comprise double-body warehouse 1 and be arranged on the grain unloading device 2 below double-body warehouse.
[0043] The double-body warehouse 1 has a first warehouse 11 and a second warehouse 12 arranged side by side. The bottom of the first warehouse is conical, and the center of the bottom has a first outlet; the bottom of the second warehouse is also conical, and the bottom of the second warehouse is conical. There is a second outlet in the center. In this embodiment, four supporting pillars 13 are arranged at the lower part of the double-body warehouse, and the double-body warehouse stands on the ground through the four supporting pillars. In practice, it is also possible not to support the pillars, but directly fix the double-body warehouse on the wall ...
Embodiment 2)
[0096] Figure 22 to Figure 25 A second embodiment of the invention is shown.
[0097] This embodiment is basically the same as Embodiment 1, the difference is: see Figure 22 to Figure 25 As shown, the side end of the limit block in this embodiment is closer to the pulley, the side end of the pulley closer to the limit block, and both sides of the clutch transmission gear are provided with gear teeth 5, Each tooth is provided with a thrust surface 51 and a guide surface 52, and each guide surface is an arc surface. When the clutch transmission gear translates toward the direction of the limit stop, the thrust surface of the gear teeth of the clutch transmission gear finally abuts against the thrust surface of the gear teeth of the limit stop; when the clutch transmission gear translates toward the direction of the pulley, the clutch The thrust bearing surface of the gear teeth of the transmission gear finally abuts against the thrust bearing surface of the gear teeth of the...
PUM
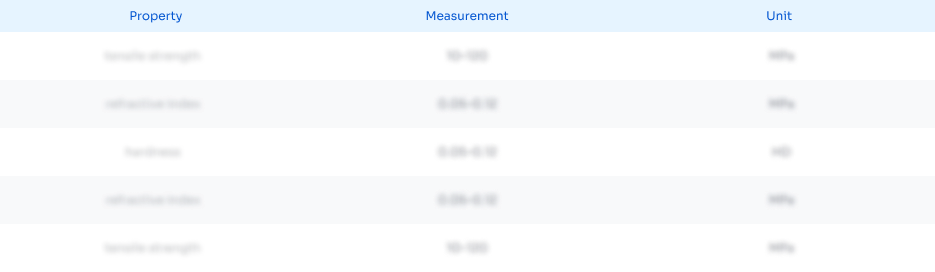
Abstract
Description
Claims
Application Information

- R&D Engineer
- R&D Manager
- IP Professional
- Industry Leading Data Capabilities
- Powerful AI technology
- Patent DNA Extraction
Browse by: Latest US Patents, China's latest patents, Technical Efficacy Thesaurus, Application Domain, Technology Topic, Popular Technical Reports.
© 2024 PatSnap. All rights reserved.Legal|Privacy policy|Modern Slavery Act Transparency Statement|Sitemap|About US| Contact US: help@patsnap.com