A method of rh rapid decarburization and reduction of molten steel temperature drop
A temperature drop and decarburization technology, applied in the field of iron and steel metallurgy, can solve the problems of low decarburization rate and large RH temperature drop, and achieve the effect of reducing the temperature drop of molten steel
- Summary
- Abstract
- Description
- Claims
- Application Information
AI Technical Summary
Problems solved by technology
Method used
Examples
Embodiment 1
[0046] 1) High-carbon drawing operation is performed at the end of converter smelting, and the carbon content at the end of converter is 0.06%, which creates conditions for RH forced decarburization.
[0047] 2) The RH oxygen blowing process is divided into two stages of forced decarburization and secondary combustion, both using a 6.6m gun position.
[0048] 3) The RH arrival temperature is 1624°C, the arrival C content is 0.04%, and the arrival O content is 400ppm. When the RH vacuum reaches 180mbar, the oxygen blowing is started, and the oxygen blowing flow rate is 2000Nm 3 / h, the oxygen blowing volume is 49m 3 .
[0049] 4) Enter the secondary combustion stage after the forced decarburization is completed. The secondary combustion is divided into 4 stages, and the flow rate of oxygen blowing is 900-500-200-100Nm 3 / h is distributed in steps, and the oxygen blowing time of each stage is 40s.
[0050] 5) When the RH end temperature is 1610°C and the RH treatment time is ...
Embodiment 2
[0052] 1) High-carbon drawing operation is performed at the end of converter smelting, and the carbon content at the end of converter is 0.07%, which creates conditions for RH forced decarburization.
[0053] 2) The RH oxygen blowing process is divided into two stages of forced decarburization and secondary combustion, both using a 6.6m gun position.
[0054] 3) The RH arrival temperature is 1621°C, the arrival C content is 0.05%, and the arrival O content is 400ppm. When the RH vacuum reaches 180mbar, the oxygen blowing is started, and the oxygen blowing flow rate is 2000Nm 3 / h, the oxygen blowing volume is 69m 3 .
[0055] 4) Enter the secondary combustion stage after the forced decarburization is completed. The secondary combustion is divided into 4 stages, and the oxygen blowing flow rate is 1000-600-300-200Nm 3 / h is distributed in steps, and the oxygen blowing time of each stage is 40s.
[0056] 5) When the RH end temperature is 1608°C and the RH treatment time is 15...
Embodiment 3
[0058] 1) High-carbon drawing operation is performed at the end of converter smelting, and the carbon content at the end of converter is 0.08%, which creates conditions for RH forced decarburization.
[0059] 2) The RH oxygen blowing process is divided into two stages of forced decarburization and secondary combustion, both using a 6.6m gun position.
[0060] 3) The RH arrival temperature is 1619°C, the arrival C content is 0.06%, and the arrival O content is 400ppm. When the RH vacuum reaches 180mbar, the oxygen blowing is started, and the oxygen blowing flow rate is 2000Nm 3 / h, the oxygen blowing volume is 88m 3 .
[0061] 4) After the forced decarburization is completed, it enters the secondary combustion stage. The secondary combustion is divided into 4 stages, and the flow rate of oxygen blowing is 1100-700-400-300Nm 3 / h is distributed in steps, and the oxygen blowing time of each stage is 40s.
[0062] 5) When the RH end temperature is 1609°C and the RH treatment ti...
PUM
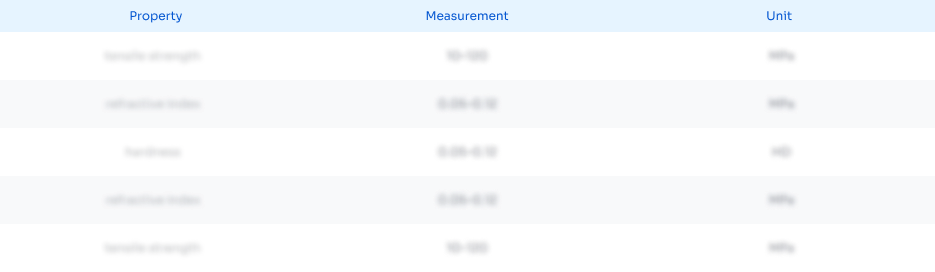
Abstract
Description
Claims
Application Information

- R&D Engineer
- R&D Manager
- IP Professional
- Industry Leading Data Capabilities
- Powerful AI technology
- Patent DNA Extraction
Browse by: Latest US Patents, China's latest patents, Technical Efficacy Thesaurus, Application Domain, Technology Topic, Popular Technical Reports.
© 2024 PatSnap. All rights reserved.Legal|Privacy policy|Modern Slavery Act Transparency Statement|Sitemap|About US| Contact US: help@patsnap.com