Ethyl alcohol processing method by clear solution of distiller grain and corn
A processing method and technology for clear liquid, which are applied in the fields of biochemical equipment and methods, liquid production bioreactors, bioreactors/fermenters for specific purposes, etc., can solve the problem of large loss rate of inorganic acid equipment and difficult processing of corn oil , the high price of corn, to achieve the effect of improving the saccharification rate, increasing the added value of the product, and reducing the saccharification time
- Summary
- Abstract
- Description
- Claims
- Application Information
AI Technical Summary
Problems solved by technology
Method used
Image
Examples
Embodiment 1
[0047] Mix the corn flour slurry after extracting part of the starch with the centrifuged clear liquid of spent distiller's grains discharged from the crude distillation tower to obtain a slurry with a corn starch concentration of 15%; add 10u / g of high-temperature-resistant α-amylase to the slurry Carry out precooking, the precooking temperature is 50°C, and the precooking time is 20 minutes. After the precooking is completed, it is heated to 95°C and maintained for 90 minutes in an aftercooker to obtain liquefied mash; the liquefied mash is pumped into the mash pot for saccharification to obtain mash mash. The amount of glucoamylase added is 200u / g, the saccharification temperature is 50°C, and the saccharification time is 20 minutes. Continuous fermentation is carried out in 5 fermentation tanks to obtain mature mash. g Add activated active dry yeast, after 12 hours of fermentation, divide about 1 / 3 of the mash from the first fermenter to the second fermenter, then refill th...
Embodiment 2
[0050] Mix the corn flour slurry after extracting part of the starch with the centrifuged clear liquid of spent distiller's grains discharged from the crude distillation tower to obtain a slurry with a corn starch concentration of 20%; add 15u / g of high-temperature-resistant α-amylase to the slurry Carry out precooking, the precooking temperature is 60°C, and the precooking time is 30 minutes. After the precooking is completed, it is heated to 105°C and maintained for 120 minutes in an aftercooker to obtain liquefied mash; the liquefied mash is pumped into the mash pot for saccharification to obtain mash mash. The amount of glucoamylase added is 250u / g. The saccharification temperature is 65°C and the saccharification time is 30 minutes. Continuous fermentation is carried out in 10 fermenters to obtain mature mash. g Add activated active dry yeast, after 16 hours of fermentation, divide about 1 / 3 of the mash from the first fermenter to the second fermenter, then refill the firs...
Embodiment 3
[0053]The corn flour slurry after extracting part of the starch is mixed with the centrifuged clear liquid of waste distiller's grains discharged from the crude distillation tower to obtain a slurry with a corn starch concentration of 17%; add 13u / g high temperature resistant α-amylase to the slurry Carry out precooking, the precooking temperature is 55°C, and the precooking time is 25 minutes. After the precooking is completed, it is heated to 100°C and maintained for 110 minutes in an aftercooker to obtain liquefied mash; the liquefied mash is pumped into the mash pot for saccharification to obtain mash mash. The amount of glucoamylase added is 220u / g. The saccharification temperature is 60°C and the saccharification time is 25 minutes. Continuous fermentation is carried out in 8 fermenters to obtain mature mash. g add activated active dry yeast, after 14 hours of fermentation, divide about 1 / 3 of the mash from the first fermenter to the second fermenter, and then refill the ...
PUM
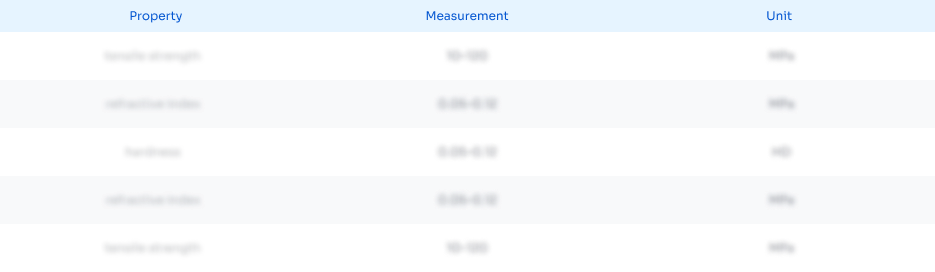
Abstract
Description
Claims
Application Information

- R&D Engineer
- R&D Manager
- IP Professional
- Industry Leading Data Capabilities
- Powerful AI technology
- Patent DNA Extraction
Browse by: Latest US Patents, China's latest patents, Technical Efficacy Thesaurus, Application Domain, Technology Topic, Popular Technical Reports.
© 2024 PatSnap. All rights reserved.Legal|Privacy policy|Modern Slavery Act Transparency Statement|Sitemap|About US| Contact US: help@patsnap.com