Internal supporting positioning device for girth welding of flange plates of carrier rocket tanks
A technology of girth welding and launch vehicle, which is applied in the direction of auxiliary devices, welding equipment, auxiliary welding equipment, etc., can solve the difficulty of flange transition joint girth welding, residual stress storage tank quality and reliability hidden dangers, assembly quality Require high-level issues to achieve the effect of improving labor productivity and safety production level, reducing workers' work environment pollution, and improving welding quality
- Summary
- Abstract
- Description
- Claims
- Application Information
AI Technical Summary
Problems solved by technology
Method used
Image
Examples
Embodiment Construction
[0026] Below in conjunction with accompanying drawing and specific embodiment the present invention is described in further detail:
[0027] This device is to ensure that when friction stir welding is used for the circular seam of the transition joint of the flange plate at the bottom of the carrier rocket storage tank, the assembly gap and the stagger amount are all less than 0.2mm, and the near gapless assembly can be realized.
[0028] like figure 1 Shown is a functional diagram of the friction stir welding positioning device for the flange transition joint of the storage tank. It can be seen from the figure that an inner support positioning device for welding the flange of the launch vehicle tank flange includes a power mechanism 1, Circumferential overall rotation mechanism 2, radial tension mechanism 3 and axial compression mechanism 4; wherein, one end of the power mechanism 1 is fixedly installed on the input end of the external planetary reducer along the shaft, and t...
PUM
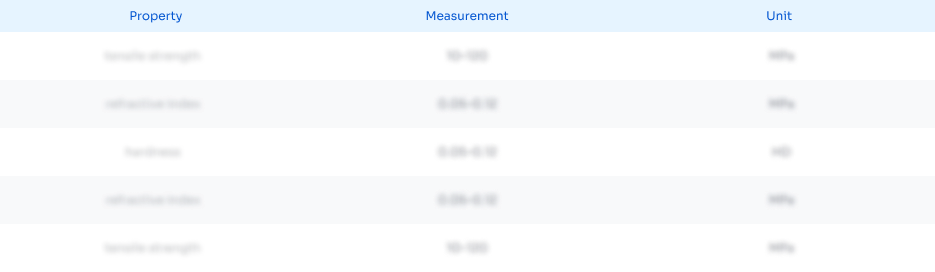
Abstract
Description
Claims
Application Information

- R&D
- Intellectual Property
- Life Sciences
- Materials
- Tech Scout
- Unparalleled Data Quality
- Higher Quality Content
- 60% Fewer Hallucinations
Browse by: Latest US Patents, China's latest patents, Technical Efficacy Thesaurus, Application Domain, Technology Topic, Popular Technical Reports.
© 2025 PatSnap. All rights reserved.Legal|Privacy policy|Modern Slavery Act Transparency Statement|Sitemap|About US| Contact US: help@patsnap.com