Method for adjusting and regulating long-periodic structure phase of magnesium alloy
A long-period structure and magnesium alloy technology, which is applied in the field of metal material preparation, can solve the problems of limiting the application of magnesium alloys, low strength of magnesium alloys, and easy oxidation corrosion, etc., and achieve the effect of reducing splitting, strengthening alloys, and eliminating LPSO phases
- Summary
- Abstract
- Description
- Claims
- Application Information
AI Technical Summary
Problems solved by technology
Method used
Image
Examples
Embodiment 1
[0039] An alloy with a chemical composition of Mg-2.8Ni-3.8Y-0.4Zr (wt.%) was prepared. Using 99.9% pure magnesium, 99.9% pure nickel, Mg-30%Y and Mg-30%Zr master alloy as raw materials, and drying at 200°C for 30min. Put the magnesium ingot into the crucible 2 in the smelting furnace 1, heat it up to 500°C for 10 minutes, and continue to heat up to 700°C. After the magnesium ingot is completely melted, add nickel chips into the melt and heat up to 770°C; after the nickel chips dissolve, add Mg-30%Zr and Mg-30%Y master alloys and keep warm for 30min; then heat up to 780°C for stirring . After all the raw materials are melted, adjust the temperature of the melt to stabilize the temperature of the melt at 730°C, then introduce high-purity argon for refining, adjust the flow of argon to ensure that the molten metal does not splash, last for 12 minutes, and remove surface scum , let stand for 30min. The whole smelting process is fed with N through the vent pipe 3 2 and SF 6 M...
Embodiment 2
[0041] An alloy with a chemical composition of Mg-1.4Zn-3.0Y-0.3Zr (wt.%) was prepared. 99.9% pure magnesium, 99.9% pure zinc, Mg-10%Y and Mg-20%Zr master alloys are used as raw materials, and dried at 150°C for 50min. First put the magnesium ingot into the crucible 2 in the smelting furnace 1, heat it up to 500°C with the furnace, keep it warm for 10 minutes, and continue to heat up to 700°C. After the magnesium ingot is completely melted, heat up to 770°C, add small pieces of zinc and Mg-30%Zr, Mg-30%Y alloys and keep warm for 30min; then heat up to 780°C for stirring. After all the raw materials are melted, adjust the temperature of the melt to 730°C, pass high-purity argon into it for refining, adjust the flow rate of argon to ensure that the molten metal does not splash, continue to ventilate for 10 minutes, then remove the surface scum, and let it stand for 30 minutes . The whole smelting process is fed with N through the vent pipe 3 2 and SF 6 Mixed gas protection. ...
Embodiment 3
[0044] An alloy with a chemical composition of Mg-1.0Ni-2.0Y (wt.%) was prepared. 99.9% pure magnesium, 99.9% pure nickel, and Mg-20% Y master alloy are used as raw materials, and dried at 200°C for 60 minutes. Put the magnesium ingot into the crucible 2 in the smelting furnace 1, heat it up to 500°C for 10 minutes, and continue to heat up to 700°C. After the magnesium ingots are completely melted, nickel chips are added to the melt, and the temperature is raised to 770°C and kept for 30 minutes; after the nickel chips are dissolved, Mg-30%Y master alloy is added and kept for 30 minutes; then the temperature is raised to 780°C for stirring. After all the raw materials are melted, adjust the temperature control of the smelting furnace to stabilize the melt temperature at 740°C, then feed high-purity argon for refining, adjust the flow of argon to ensure that the molten metal does not splash, last for 15 minutes, and remove the surface Scum, let stand for 40min. The whole smel...
PUM
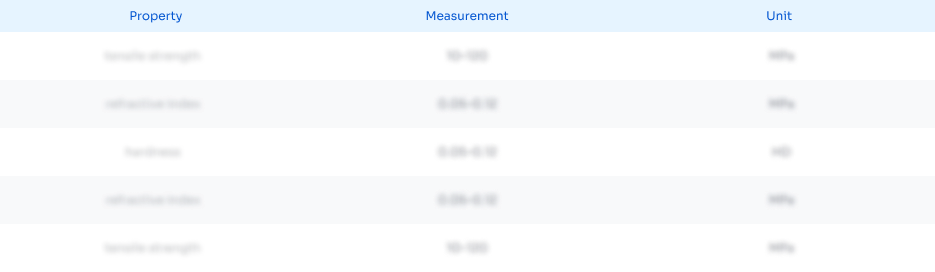
Abstract
Description
Claims
Application Information

- R&D
- Intellectual Property
- Life Sciences
- Materials
- Tech Scout
- Unparalleled Data Quality
- Higher Quality Content
- 60% Fewer Hallucinations
Browse by: Latest US Patents, China's latest patents, Technical Efficacy Thesaurus, Application Domain, Technology Topic, Popular Technical Reports.
© 2025 PatSnap. All rights reserved.Legal|Privacy policy|Modern Slavery Act Transparency Statement|Sitemap|About US| Contact US: help@patsnap.com