Automatic double-head tube end forming machine
A double-head pipe and forming machine technology, applied in the direction of feeding device, manufacturing tool, positioning device, etc., can solve the problems of pipe clamp positioning influence, affecting pipe forming accuracy, etc., to improve stability, prevent material jamming, and scientific structure reasonable effect
- Summary
- Abstract
- Description
- Claims
- Application Information
AI Technical Summary
Problems solved by technology
Method used
Image
Examples
Embodiment 1
[0026] Embodiment 1: an automatic double-head pipe end forming machine, comprising a body 1, a vibration plate 2, a feeding device 3, a clamping device 4 and a forming device 5, the vibration plate 2 is fixed on the body 1, and the vibration The disc 2 communicates with the feeding device 3 through the feed pipe 6;
[0027] The feeding device 3 includes a push seat 31, a push arm 32, a first drive device 33 and a fourth drive device 34, the first drive device 33 is fixedly connected to the fuselage 1, and the push arm 32 is connected to the first drive device 33 connection, the push arm 32 is provided with two parallel push rods 321, the head of each push rod is provided with an inclined rod head 322, and the middle part of each push rod 321 is provided with a first material seat 323, and the push rod 321 is provided with a first material seat 323. The upper end of the seat 31 is provided with a second material seat 311, the second material seat material 311 is connected to tw...
Embodiment 2
[0032] Embodiment 2: The difference from Embodiment 1 is that the forming part 51 includes a fixed part 53, a rotating part 54 and a servo motor 55, the fixed part 53 is fixedly connected to the servo motor 55, and the rotating part 54 is connected to the servo motor 55. The rotating shaft 551 of the servo motor 55 is connected, and the rotating part 54 is provided with two molding dies 511 (the number of molding dies in this embodiment is two, but not limited to two, it can be more than two); working principle and embodiment 1 is that the servo motor 55 can control the rotation of the rotating part 54, and rotate and replace the forming mold 511 as required.
PUM
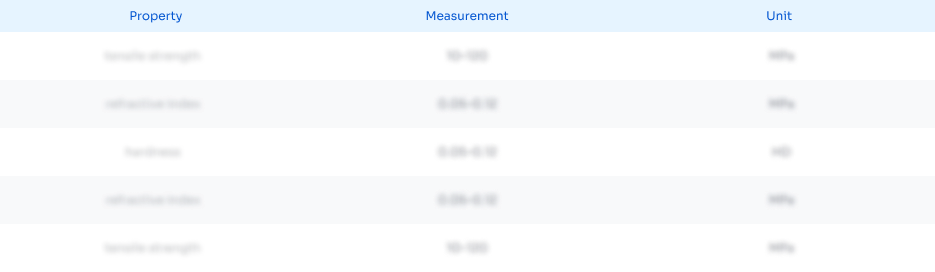
Abstract
Description
Claims
Application Information

- Generate Ideas
- Intellectual Property
- Life Sciences
- Materials
- Tech Scout
- Unparalleled Data Quality
- Higher Quality Content
- 60% Fewer Hallucinations
Browse by: Latest US Patents, China's latest patents, Technical Efficacy Thesaurus, Application Domain, Technology Topic, Popular Technical Reports.
© 2025 PatSnap. All rights reserved.Legal|Privacy policy|Modern Slavery Act Transparency Statement|Sitemap|About US| Contact US: help@patsnap.com