Sendust/ferrite composite magnetic powder and preparation method of magnetic powder core adopting same
A technology of sendust and ferrite, which is applied in the field of material preparation, can solve problems such as improving magnetic permeability, low core loss, and unstable strength of the insulating layer, so as to improve magnetic permeability and resistivity, and reduce high frequency Eddy current loss, the effect of overcoming the instability of the insulating layer
- Summary
- Abstract
- Description
- Claims
- Application Information
AI Technical Summary
Problems solved by technology
Method used
Examples
preparation example Construction
[0024] The invention provides a method for preparing sendust / ferrite composite magnetic powder, comprising the following steps:
[0025] 1) Iron, silicon, and aluminum raw materials are made into a sendust strip of standard composition, which is then crushed and ball-milled to obtain flat sendust magnetic powder; the Fe 3+ , Zn 3+ and Mn 2+ The nitrate is fully dissolved in deionized water to obtain Fe-Zn-Mn mixed nitrate solution;
[0026] 2) Add a corresponding amount of the sendust magnetic powder into the Fe-Zn-Mn mixed nitrate solution according to the coating amount (theoretical calculation value) of ferrite in the sendust / ferrite composite magnetic powder, at 120 Conduct hydrothermal reaction at ℃~220℃ for 5h~11h, add NaOH solution, adjust the pH value to 8~12, generate manganese zinc ferrite on the surface of sendust magnetic powder in situ, wash and dry in turn to obtain iron silicon Aluminum / ferrite composite magnetic powder.
[0027] In the preparation method of...
Embodiment 1
[0041] In this embodiment, the composition of the sendust magnetic powder is Si: 9.6 wt%, Al: 5.4 wt%, and the rest is Fe.
[0042] 1) Using an induction-type melt quenching device, in a directional magnetic field of 1000Oe, iron, silicon, and aluminum raw materials are made into iron-silicon-aluminum alloy strips with standard components, then crushed, and placed in a ball mill for high-energy ball milling, wherein, The ball-to-material ratio is 12:1, and the ball mill is 40h to obtain flattened sendust magnetic powder; Fe 3+ , Zn 3+ and Mn 2+ of nitrates as raw materials, according to Fe 3+ , Zn 2+ and Mn 2+ The mol ratio is 10:3:2 weighing, adding deionized water to fully dissolve, obtain Fe-Zn-Mn mixed nitrate solution;
[0043] 2) The sendust magnetic powder is added to the mixed nitrate solution according to the mass ratio of manganese zinc ferrite and sendust magnetic powder at a mass ratio of 6%, and the pH value is adjusted to 10 with a NaOH solution having a con...
Embodiment 2
[0053] In this embodiment, the composition of the sendust magnetic powder is Si: 9.6 wt%, Al: 5.4 wt%, and the rest is Fe.
[0054] 1) Using an induction-type melt quenching device, in a directional magnetic field of 1000Oe, iron, silicon, and aluminum raw materials are made into iron-silicon-aluminum alloy strips with standard components, then crushed, and placed in a ball mill for high-energy ball milling, wherein, The ball-to-material ratio is 12:1, and the ball mill is 40h to obtain flattened sendust magnetic powder; Fe 3+ , Zn 3+ and Mn 2+ of nitrates as raw materials, according to Fe 3+ , Zn 2+ and Mn 2+ The mol ratio is 10:3:2 weighing, fully dissolved in deionized water, obtain Fe-Zn-Mn mixed nitrate solution;
[0055] 2) The sendust magnetic powder is added to the mixed nitrate solution according to the mass ratio of manganese zinc ferrite and sendust magnetic powder at a mass ratio of 6%, and the pH value is adjusted to 10 with a NaOH solution having a concentra...
PUM
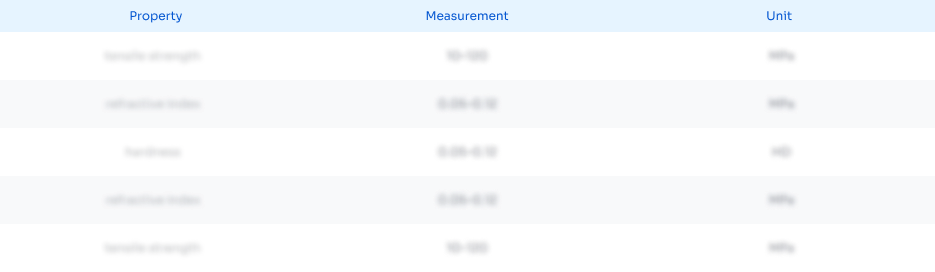
Abstract
Description
Claims
Application Information

- R&D
- Intellectual Property
- Life Sciences
- Materials
- Tech Scout
- Unparalleled Data Quality
- Higher Quality Content
- 60% Fewer Hallucinations
Browse by: Latest US Patents, China's latest patents, Technical Efficacy Thesaurus, Application Domain, Technology Topic, Popular Technical Reports.
© 2025 PatSnap. All rights reserved.Legal|Privacy policy|Modern Slavery Act Transparency Statement|Sitemap|About US| Contact US: help@patsnap.com