Preparation method of high-quality AlV55 alloy
A high-quality, alloyed technology, applied in the field of metallurgy, to achieve the effect of reducing carbon content, reducing contact, and avoiding excessive heat concentration
- Summary
- Abstract
- Description
- Claims
- Application Information
AI Technical Summary
Problems solved by technology
Method used
Image
Examples
Embodiment 1
[0032] Mix 3kg of vanadium trioxide, 2.75kg of aluminum, and 1.92kg of calcium oxide, take out 1 / 4 of the raw materials, mix in potassium chlorate as the base material, make the calorific value of the base material reach 3100kJ / kg, put the base material into the furnace and ignite After the molten pool is stabilized, lower the electrode to smelt, and then add the remaining raw materials in batches. After all the raw materials are filled, spray 32.4g of aluminum-calcium alloy into the molten slag, let it stand for 5min, and spray 185g of alloy into the alloy. Refining agent, let stand for 10min. After the reaction, 3.46kg of vanadium-aluminum alloy was obtained, the recovery rate of vanadium reached 97.01%, and the alloy impurity content reached the AlV50 vanadium-aluminum alloy standard of German GfE company. The main components of the alloy are shown in Table 1.
[0033] V Al Fe Si C P Cr 57.15 42.35 0.14 0.10 0.07 0.015 0.006 S B Cu Mg ...
Embodiment 2
[0035] Mix 10kg of vanadium trioxide, 9.3kg of aluminum, and 6.6kg of calcium oxide, take out 1 / 4 of the raw materials, mix in potassium chlorate as the base material, make the calorific value of the base material reach 3100kJ / kg, put the base material into the furnace and ignite After the molten pool is stabilized, lower the electrodes and smelt with electricity, and then add the remaining raw materials in batches. After all the raw materials are filled, spray 100g of aluminum-calcium alloy into the molten slag, let it stand for 6 minutes, and spray 500g of alloy into the alloy for refining. agent, let it stand for 15 minutes. After the reaction finished, 11.5kg of vanadium-aluminum alloy was obtained, the recovery rate of vanadium reached more than 97%, and the alloy impurity content reached the AlV50 vanadium-aluminum alloy standard of German GfE company. The main components of the alloy are shown in Table 2.
[0036] V Al Fe Si C P Cr 57.81 41.72 0....
Embodiment 3
[0038]Mix 5kg of vanadium trioxide, 4.6kg of aluminum, and 3.3kg of calcium oxide, take out 1 / 5 of the raw materials, mix in potassium chlorate as the base material, make the calorific value of the base material reach 3200kJ / kg, put the base material into the furnace and ignite After the molten pool is stabilized, lower the electrode to smelt, and then add the remaining raw materials in batches. After all the raw materials are filled, spray 50g of aluminum-calcium alloy into the molten slag, let it stand for 5min, and spray 300g of alloy into the alloy for refining. agent, let it stand for 10 minutes. After the reaction finished, 5.74kg of vanadium-aluminum alloy was obtained, the recovery rate of vanadium reached more than 97%, and the alloy impurity content reached the AlV50 vanadium-aluminum alloy standard of German GfE company. The main components of the alloy are shown in Table 3.
[0039] V Al Fe Si C P Cr 56.85 42.71 0.13 0.08 0.06 0.011 0.00...
PUM
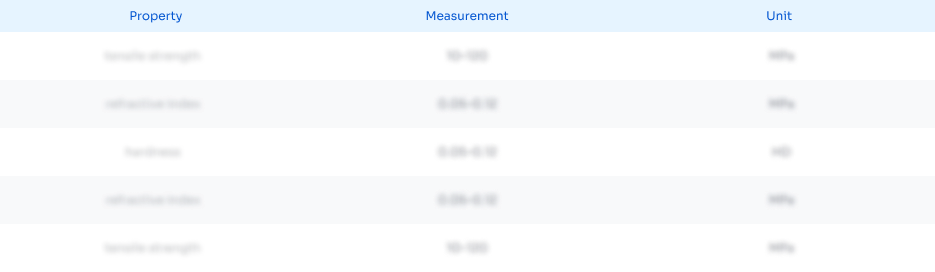
Abstract
Description
Claims
Application Information

- Generate Ideas
- Intellectual Property
- Life Sciences
- Materials
- Tech Scout
- Unparalleled Data Quality
- Higher Quality Content
- 60% Fewer Hallucinations
Browse by: Latest US Patents, China's latest patents, Technical Efficacy Thesaurus, Application Domain, Technology Topic, Popular Technical Reports.
© 2025 PatSnap. All rights reserved.Legal|Privacy policy|Modern Slavery Act Transparency Statement|Sitemap|About US| Contact US: help@patsnap.com