Preparation method of ultrahigh-conductivity 3D printing carbon fiber composite wire
A 3D printing and composite wire technology, applied in the field of 3D printing materials, can solve the problems of mechanical properties and mechanical properties that need to be improved, unsuitable for 3D printing, etc., and achieve the effect of simple and feasible preparation process, good melt processability, and high strength.
- Summary
- Abstract
- Description
- Claims
- Application Information
AI Technical Summary
Problems solved by technology
Method used
Examples
Embodiment 1
[0016] The present invention provides a preparation method for 3D printing super high-conductivity carbon fiber composite wire. The materials are calculated by weight. The specific steps include:
[0017] (1) Put 60 parts of polyamide resin, 5 parts of boron trifluoride monoethylamine, 5 parts of antioxidant, 2 parts of nanoparticle carrier type catalyst, 2 parts of color masterbatch, and 4 parts of processing aids on a vacuum drum at 150℃ Dry in the drying box for 3 hours, then cool to room temperature for later use;
[0018] (2) Put 1 part of AG80 epoxy resin and the dry and mixed plastic materials in step (1) into a high-speed kneader and mix for 2 minutes;
[0019] (3) Then the raw materials mixed in step (2) in the high-speed kneader are put into the hopper of the twin-screw extruder, 60 parts of carbon fiber are added to the extruder through the side feed, and they are melted, extruded and cast. Belting, drawing and winding; the processing technology is as follows: twin-screw ...
Embodiment 2
[0021] The present invention provides a preparation method for 3D printing super high-conductivity carbon fiber composite wire. The materials are calculated by weight. The specific steps include:
[0022] (1) Put 63 parts of polyphenylene sulfide resin, 6 parts of boron trifluoride monoethylamine, 1 part of antioxidant, 4 parts of nanoparticle carrier catalyst, 3 parts of color masterbatch, and 5 parts of processing aids in a vacuum at 150℃ Dry in a drum drying box for 4 hours, then cool to room temperature for later use;
[0023] (2) Put 2 parts of AG80 epoxy resin and the dry and mixed plastic materials in step (1) into a high-speed kneader and mix for 4 minutes;
[0024] (3) Then the raw materials mixed in step (2) in the high-speed kneader are put into the hopper of the twin-screw extruder, and 65 parts of carbon fiber are added to the extruder through the side feed. Belting, drawing, winding; the processing technology is as follows: the temperature of the first zone of the twin...
Embodiment 3
[0026] The present invention provides a preparation method for 3D printing super high-conductivity carbon fiber composite wire. The materials are calculated by weight. The specific steps include:
[0027] (1) Put 64 parts of polyether ether ketone resin, 5 parts of boron trifluoride monoethylamine, 1 part of antioxidant, 4 parts of nanoparticle carrier catalyst, 4 parts of color masterbatch, and 5 parts of processing aids in a vacuum at 150℃ Dry in a drum drying box for 4 hours, then cool to room temperature for later use;
[0028] (2) Put 3 parts of AG80 epoxy resin and the dry and mixed plastic materials in step (1) into a high-speed kneader and mix for 4 minutes;
[0029] (3) Then the raw materials mixed in step (2) in the high-speed kneader are put into the hopper of the twin-screw extruder, 70 parts of carbon fiber are added to the extruder through the side feed, and then melted, extruded and cast. Belting, drawing, winding; the processing technology is as follows: the temperat...
PUM
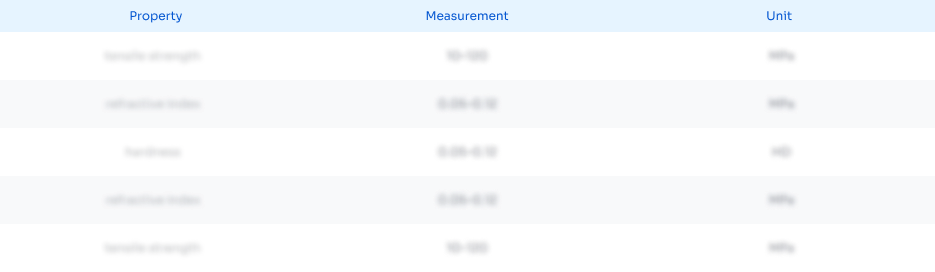
Abstract
Description
Claims
Application Information

- R&D
- Intellectual Property
- Life Sciences
- Materials
- Tech Scout
- Unparalleled Data Quality
- Higher Quality Content
- 60% Fewer Hallucinations
Browse by: Latest US Patents, China's latest patents, Technical Efficacy Thesaurus, Application Domain, Technology Topic, Popular Technical Reports.
© 2025 PatSnap. All rights reserved.Legal|Privacy policy|Modern Slavery Act Transparency Statement|Sitemap|About US| Contact US: help@patsnap.com