Economic and environmentally friendly method for producing invar steel wire rod coils
A production method and wire rod technology, applied in the field of Invar cold heading and hot rolling wire rod coiling, can solve the problems of material acid damage, material surface erosion, and economic loss of enterprises, so as to reduce the risk factor, improve surface quality, and market The effect of increased competition
- Summary
- Abstract
- Description
- Claims
- Application Information
AI Technical Summary
Problems solved by technology
Method used
Examples
Embodiment 1
[0020] The production method of Invar wire rod coiling in this embodiment includes: first coiling the hot-rolled wire rod without pickling, after hanging the lubricating ash, cold drawing one line until the material is round, and the cold drawn wire rod, using Annealing in an atmosphere hood-type protective furnace, annealing temperature 930°C, heat preservation for 3 hours, cooling to below 200°C with the furnace, and peeling 1mm in radial direction after straightening in a peeling machine. Specifically, use the disc peeling machine (JY20 type) produced by Taizhou Haobang Technology Development Co., Ltd., or the PB6 / 20P hot-rolled disc peeling machine produced by Yantai Hangjian Special Steel Finishing Equipment Co., Ltd. for direct peeling without pickling .
Embodiment 2
[0022] The production method of Invar wire rod coiling in this embodiment includes: first coiling the hot-rolled wire rod without pickling, after hanging the lubricating ash, cold drawing one line until the material is round, and the cold drawn wire rod, using Annealing in an atmosphere hood-type protection furnace, annealing temperature 920°C, heat preservation for 3.5 hours, cooling to below 200°C with the furnace, leaving the furnace, straightening in a peeling machine, and peeling 1.05mm in radial direction. Specifically, use the disc peeling machine (JY20 type) produced by Taizhou Haobang Technology Development Co., Ltd., or the PB6 / 20P hot-rolled disc peeling machine produced by Yantai Hangjian Special Steel Finishing Equipment Co., Ltd. for direct peeling without pickling .
Embodiment 3
[0024] The production method of Invar wire rod coiling in this embodiment includes: first coiling the hot-rolled wire rod without pickling, after hanging the lubricating ash, cold drawing one line until the material is round, and the cold drawn wire rod, using Annealing in an atmosphere hood-type protective furnace, annealing temperature 940°C, heat preservation for 2.5 hours, cooling to below 200°C with the furnace, leaving the furnace, straightening in a peeling machine, and peeling 0.95mm in radial direction. Specifically, use the disc peeling machine (JY20 type) produced by Taizhou Haobang Technology Development Co., Ltd., or the PB6 / 20P hot-rolled disc peeling machine produced by Yantai Hangjian Special Steel Finishing Equipment Co., Ltd. for direct peeling without pickling .
PUM
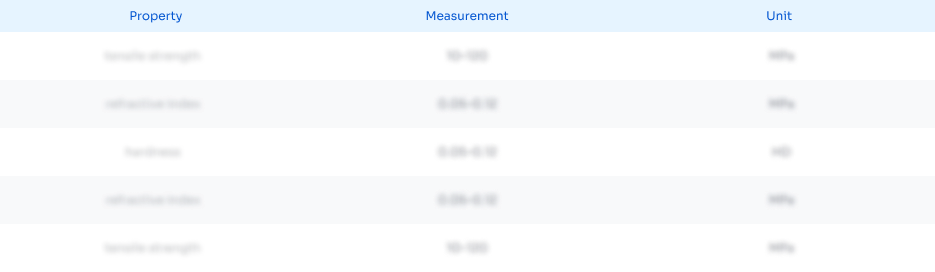
Abstract
Description
Claims
Application Information

- R&D Engineer
- R&D Manager
- IP Professional
- Industry Leading Data Capabilities
- Powerful AI technology
- Patent DNA Extraction
Browse by: Latest US Patents, China's latest patents, Technical Efficacy Thesaurus, Application Domain, Technology Topic, Popular Technical Reports.
© 2024 PatSnap. All rights reserved.Legal|Privacy policy|Modern Slavery Act Transparency Statement|Sitemap|About US| Contact US: help@patsnap.com