Non-asbestos high-temperature-resistant clutch surface patch and manufacturing method thereof
A clutch face, high temperature resistance technology, applied in the field of friction materials, can solve the problems of decreased mechanical strength, poor heat resistance of asbestos, poor wear resistance, etc., and achieves the effect of reducing friction coefficient, eliminating pollution hazards and low wear and tear.
- Summary
- Abstract
- Description
- Claims
- Application Information
AI Technical Summary
Problems solved by technology
Method used
Image
Examples
Embodiment 1
[0028] Embodiment 1: Preparation of asbestos-free high temperature resistant clutch face
[0029] Raw material weight ratio: modified glass fiber, 30 parts; copper fiber, 7 parts; aramid fiber, 4 parts; nitrile rubber, 25 parts; phenolic resin, 15 parts; vulcanizing agent, 3 parts; anti-aging agent, 4 parts ; graphite, 12 parts; barite powder, 10 parts; nano silicon dioxide, 7 parts; nano titanium dioxide, 4 parts.
[0030] The preparation method of described modified glass fiber comprises the steps:
[0031] Step S1, immerse the glass fiber in the bottom film solution for 2 hours, the soaking temperature is 50°C, take it out after soaking and bake it at 80°C for 3 hours, that is, cover a layer of bottom film on the surface of the glass fiber; the bottom film solution is ethylene 260g of vinyltriethoxysilane, 50g of p-toluidine and 150g of nonylphenol ethoxylate per liter of ethanol solution ;
[0032] Step S2, immerse the glass fiber covered with the bottom film in the pol...
Embodiment 2
[0039] Embodiment 2: Preparation of asbestos-free high temperature resistant clutch face
[0040] Raw material weight ratio: modified glass fiber, 25 parts; copper fiber, 6 parts; aramid fiber, 3 parts; nitrile rubber, 20 parts; phenolic resin, 10 parts; vulcanizing agent, 2 parts; anti-aging agent, 3 parts ; graphite, 10 parts; barite powder, 8 parts; nano silicon dioxide, 6 parts; nano titanium dioxide, 3 parts.
[0041] The preparation method of described modified glass fiber comprises the steps:
[0042]Step S1, immerse the glass fibers in the bottom film solution for 1 hour, the soaking temperature is 55°C, take out after soaking and bake at 70°C for 4 hours, that is, cover a layer of bottom film on the surface of the glass fiber; the bottom film solution is ethylene 240g vinyltriethoxysilane, 45g p-toluidine and 130g nonylphenol ethoxylate per liter of ethanol solution ;
[0043] Step S2, immerse the glass fiber covered with the bottom film in the polymer solution for...
Embodiment 3
[0050] Embodiment 3: Preparation of asbestos-free high temperature resistant clutch face
[0051] Raw material weight ratio: modified glass fiber, 35 parts; copper fiber, 8 parts; aramid fiber, 5 parts; nitrile rubber, 30 parts; phenolic resin, 20 parts; vulcanizing agent, 4 parts; anti-aging agent, 5 parts ; graphite, 14 parts; barite powder, 12 parts; nano silicon dioxide, 8 parts; nano titanium dioxide, 5 parts.
[0052] The preparation method of described modified glass fiber comprises the steps:
[0053] Step S1, immerse the glass fiber in the bottom film solution for 3 hours, the soaking temperature is 45°C, take it out after soaking and bake it at 90°C for 2 hours, that is, cover a layer of bottom film on the surface of the glass fiber; the bottom film solution is ethylene 280g of vinyltriethoxysilane, 55g of p-toluidine and 170g of nonylphenol ethoxylate per liter of ethanol solution ;
[0054] Step S2, immerse the glass fiber covered with the bottom film in the pol...
PUM
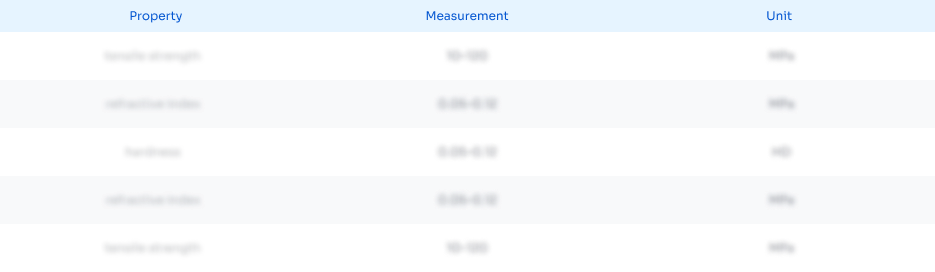
Abstract
Description
Claims
Application Information

- Generate Ideas
- Intellectual Property
- Life Sciences
- Materials
- Tech Scout
- Unparalleled Data Quality
- Higher Quality Content
- 60% Fewer Hallucinations
Browse by: Latest US Patents, China's latest patents, Technical Efficacy Thesaurus, Application Domain, Technology Topic, Popular Technical Reports.
© 2025 PatSnap. All rights reserved.Legal|Privacy policy|Modern Slavery Act Transparency Statement|Sitemap|About US| Contact US: help@patsnap.com