A production process of multi-wall thickness and multi-standard precision square tubes for photoelectric tubes
A production process and multi-standard technology, which is applied in the field of production process of multi-wall thickness and multi-standard precision square tubes for photoelectric tubes, can solve the problem that the thermal stability and safety of the shell cannot be effectively guaranteed, the shell cannot fully adapt to the working environment, the shell Frequent changes in body working temperature and other problems, to achieve the effects of convenient and controllable production, shortened calculation amount, and high degree of automation
- Summary
- Abstract
- Description
- Claims
- Application Information
AI Technical Summary
Problems solved by technology
Method used
Examples
Embodiment 1
[0021] A kind of square tube 8.0mm * 8.0mm for photoelectric tubes, a precision square tube production process with a wall thickness of 1.0mm, comprising the following steps:
[0022] Step 1. Customized process design, select special tube blanks, according to the external dimensions A, B and D of square tube products, where A and B represent length and width, and D represents wall thickness, the dimensions of the selected special tube blanks are Φ and D. 0 , where Φ is the diameter, D 0 is the wall thickness, Φ 2 =A 2 +B 2 , after sizing and walling the special tube billet, hot extrusion is carried out, and then cold rolling is carried out several times to reach the required size of the finished square tube, and then one pass of empty drawing is carried out, and the peripheral compression coefficient η is 1.08, after one pass of empty drawing is completed, one pass of mold drawing deformation is carried out, and the peripheral compression coefficient η value is 1.12, and t...
Embodiment 2
[0027] A kind of square tube 10.0mm * 10.0mm for photoelectric tubes, a precision square tube production process with a wall thickness of 1.0mm, comprising the following steps:
[0028] Step 1. Customized process design, select special tube blanks, according to the external dimensions A, B and D of square tube products, where A and B represent length and width, and D represents wall thickness, the dimensions of the selected special tube blanks are Φ and D. 0 , where Φ is the diameter, D 0 is the wall thickness, Φ 2 =A 2 +B 2 , after sizing and walling the special tube billet, hot extrusion is carried out, and then cold rolling is carried out several times to reach the required size of the finished square tube, and then one pass of empty drawing is carried out, and the peripheral compression coefficient η is 1.16. After one pass of empty drawing is completed, one pass of mold drawing deformation is carried out, and the peripheral compression coefficient η value is 1.15, and...
Embodiment 3
[0033] A kind of square tube 13.0mm * 13.0mm for photoelectric tubes, a precision square tube production process with a wall thickness of 0.7mm, comprising the following steps:
[0034] Step 1. Customized process design, select special tube blanks, according to the external dimensions A, B and D of square tube products, where A and B represent length and width, and D represents wall thickness, the dimensions of the selected special tube blanks are Φ and D. 0 , where Φ is the diameter, D 0 is the wall thickness, Φ 2 =A 2 +B 2 , for the special tube billet, the round tube is sized and the wall is fixed, and after hot extrusion and cold rolling for many times, it reaches the required size of the finished square tube, and then one pass of empty drawing is carried out. The peripheral compression coefficient η value is 1.08, and one pass After the first empty drawing is completed, the second pass of mold drawing deformation is carried out, the elongation coefficient is 1.170, an...
PUM
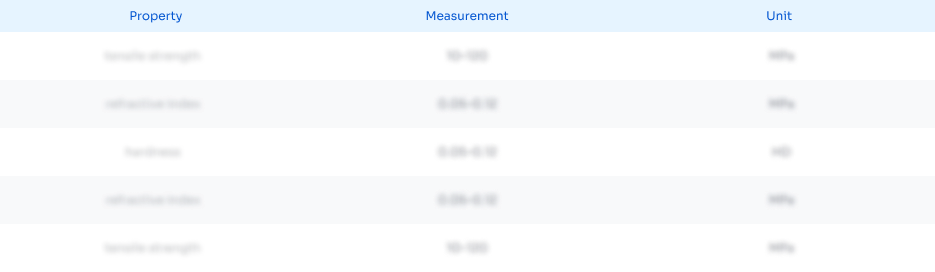
Abstract
Description
Claims
Application Information

- R&D Engineer
- R&D Manager
- IP Professional
- Industry Leading Data Capabilities
- Powerful AI technology
- Patent DNA Extraction
Browse by: Latest US Patents, China's latest patents, Technical Efficacy Thesaurus, Application Domain, Technology Topic, Popular Technical Reports.
© 2024 PatSnap. All rights reserved.Legal|Privacy policy|Modern Slavery Act Transparency Statement|Sitemap|About US| Contact US: help@patsnap.com