Method for manufacturing force responsive photonic crystal materials based on inverse compressing nano-forming technology
A nano-molding technology and photonic crystal technology, which is applied in the field of preparation of force-responsive photonic crystal materials, can solve the problems of difficulty in preparing nano-scale photonic crystals, limited precision of photonic crystals, poor structure controllability, etc., and achieve shortening The effect of preparation cycle, short preparation cycle, and reduction of preparation cost
- Summary
- Abstract
- Description
- Claims
- Application Information
AI Technical Summary
Problems solved by technology
Method used
Image
Examples
Embodiment 1
[0050] The preparation method of the force-responsive photonic crystal is as follows:
[0051] 1. If figure 1 As shown, the preparation steps of the quartz mother template are as follows:
[0052] (1) According to actual needs, pre-design the structural parameters of photonic crystals, mainly including: the surface structure is a hexagonal columnar lattice, the lattice period is 200nm, the diameter of the raised columns is 100nm, and the height of the raised columns is 150nm. The effective area is 20×20mm 2 .
[0053] (2) Take a piece of quartz substrate (size is 25mm×25mm), according to the structural parameters of the above photonic crystal, use electron beam lithography technology to expose the quartz substrate and the photoresist on it for 30s, and obtain a strip after development. A photoresist with a design pattern; then, use reactive ion etching technology to etch the quartz substrate and the photoresist on it for 20 minutes, in order to accurately transfer the patte...
PUM
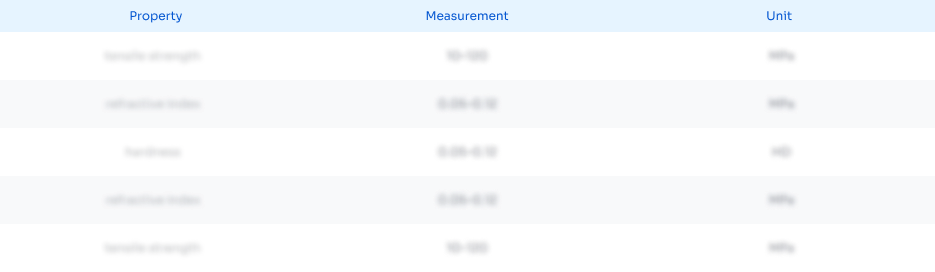
Abstract
Description
Claims
Application Information

- R&D
- Intellectual Property
- Life Sciences
- Materials
- Tech Scout
- Unparalleled Data Quality
- Higher Quality Content
- 60% Fewer Hallucinations
Browse by: Latest US Patents, China's latest patents, Technical Efficacy Thesaurus, Application Domain, Technology Topic, Popular Technical Reports.
© 2025 PatSnap. All rights reserved.Legal|Privacy policy|Modern Slavery Act Transparency Statement|Sitemap|About US| Contact US: help@patsnap.com