Steel-slag inflaming-retarding heat-preservation foam concrete and preparing method thereof
A foamed concrete, flame retardant and thermal insulation technology, applied in ceramic products, other household appliances, sustainable waste treatment, etc., can solve the problems of steel slag water washing ball mill tail mud, difficult to transport and stack, pollute the production site and other problems, to reduce floating Chance of merging, water consumption reduction, effect of reducing water absorption
- Summary
- Abstract
- Description
- Claims
- Application Information
AI Technical Summary
Problems solved by technology
Method used
Image
Examples
Embodiment 1
[0042] Example 1: The flame-retardant and heat-retaining foam concrete is prepared according to the mass ratio of various raw materials: 40 parts of cement, 42 parts of fly ash, 18 parts of mineral powder, 0.2 part of melamine water reducer, 0.03 parts of 10,000-viscosity cellulose ether part, 0.2 part of silane water-repellent agent, 4.8 parts of gypsum, 0.08 part of polypropylene fiber, 0.20 part of plant protein foaming agent, and 0.33 part of water; the preparation method is: first cement, fly ash, mineral powder, Modified component water reducer, cellulose ether, water repellent, gypsum, and polypropylene fiber are mixed evenly to obtain dry powder; the foaming agent is diluted with water, and the foaming agent aqueous solution is made into foam by an air compression foaming machine Add appropriate amount of water to the dry powder and mix it. It is required that the slurry is uniform without agglomeration and large particles. Take the prepared foam and add it to the cemen...
Embodiment 2
[0043] Example 2: The flame-retardant and heat-retaining foam concrete is prepared according to the mass ratio of various raw materials: 50 parts of cement, 25 parts of fly ash, 25 parts of mineral powder, 0.4 part of naphthalene-based water reducer, 20,000-viscosity cellulose ether 0.03 part, 0.4 part of siloxane water-repellent agent, 2 parts of gypsum, 0.16 part of polypropylene fiber, 0.21 part of animal protein foaming agent, 0.31 part of water; Its preparation method is with embodiment 1.
Embodiment 3
[0044] Example 3: The flame-retardant and heat-retaining foam concrete is prepared according to the mass ratio of various raw materials: 60 parts of cement, 12 parts of fly ash, 28 parts of mineral powder, 0.3 part of naphthalene-based water reducer, 20,000-viscosity cellulose ether 0.05 part, 0.2 part of siloxane water-repellent agent, 1.2 part of gypsum, 0.24 part of polypropylene fiber, 0.20 part of animal protein foaming agent, 0.32 part of water; Its preparation method is with embodiment 1.
PUM
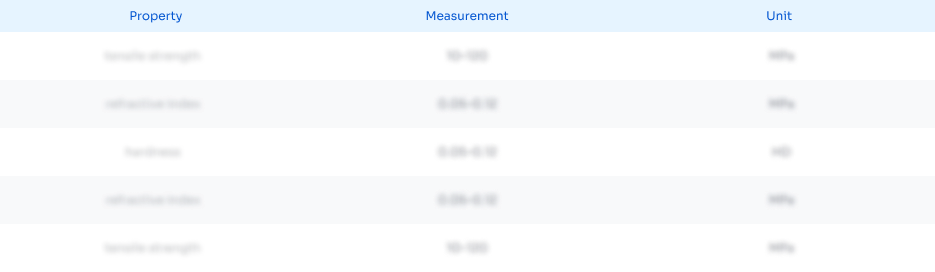
Abstract
Description
Claims
Application Information

- R&D
- Intellectual Property
- Life Sciences
- Materials
- Tech Scout
- Unparalleled Data Quality
- Higher Quality Content
- 60% Fewer Hallucinations
Browse by: Latest US Patents, China's latest patents, Technical Efficacy Thesaurus, Application Domain, Technology Topic, Popular Technical Reports.
© 2025 PatSnap. All rights reserved.Legal|Privacy policy|Modern Slavery Act Transparency Statement|Sitemap|About US| Contact US: help@patsnap.com