Method for preparing ethylenediamine esilate
A technology of ethylenediaminoethanesulfonate and ethylenediaminoethanesulfonate, applied in the direction of sulfonate preparation, chemical instruments and methods, catalyst activation/preparation, etc., can solve the problem of harsh reaction conditions and conversion rate Not high, high reaction temperature and other problems, to achieve the effect of mild reaction conditions, high controllability, excellent activity and stability, and improved sulfonic acid resistance
- Summary
- Abstract
- Description
- Claims
- Application Information
AI Technical Summary
Problems solved by technology
Method used
Image
Examples
Embodiment 1
[0057] (1), 75.82 grams of bauxite, 9 grams of cellulose derivative compounds, and 4.5 grams of nitric acid solution were mixed and kneaded until plastic, dried and roasted after extrusion to obtain a catalyst carrier;
[0058] (2) 19.42 grams of nickel nitrate, 19.46 grams of cobalt nitrate, 1.03 grams of manganese nitrate, 0.74 grams of molybdenum nitrate, and 0.34 grams of technetium nitrate are added to deionized water to obtain a co-impregnation solution, and trimethylamine is used to adjust pH=10.5, and then the The carrier was impregnated for 3 hours at a temperature of 25°C; the drying time was 10 hours at a drying temperature of 95°C; the firing temperature was 450°C for 1.5 hours. The active component in the obtained hydrogenation catalyst is NiO 5wt%, CoO5wt%, Mo 2 o 3 0.2wt%, MnO 2 0.5wt%,Tc 2 0 7 0.1wt%, others as a carrier of 100 g pre-reforming hydrogenation catalyst 1.
[0059] (3) Fill the pre-reforming hydrogenation catalyst into a 400 milliliter hydr...
Embodiment 2-5
[0061] Change the ratio of nickel nitrate, cobalt nitrate, manganese nitrate, molybdenum nitrate and technetium nitrate, and the carrier, other conditions are basically the same as in the examples, and catalyst 2-5 is prepared. The content of active components is shown in Table 1, and the content is based on The total mass of the catalyst, and the rest of the components are carriers.
[0062] Table 1 Catalyst 1-5 Composition Table
[0063]
Embodiment 6
[0065] 147 grams of sodium taurine (1mol) are placed in the there-necked flask equipped with stirrer, thermometer, dropping funnel, slowly drip 114 grams (1mol) of 50wt% hydroxyacetonitrile aqueous solution by dropping funnel under stirring, keep reaction The temperature was at 30°C, the time for dropping was 30 minutes, and then the reaction was incubated for 20 minutes. The reaction liquid was removed by rotary evaporation under reduced pressure to remove water, and dried at 90°C for 3 hours to obtain 183.21 grams of light yellow crystal sodium cyanoethyl taurate. The yield was 98.5%.
[0066] Get 100 grams of sodium cyanoethyl taurate and dissolve it in 870 grams of dioxane, and add 30 grams of liquid ammonia using a high-pressure pump,
[0067] Fill 100 grams of hydrogenation catalyst 1 into a high-pressure hydrogenation fixed bed, press it to 10 MPa (gauge pressure) after hydrogen replacement, keep warm at a temperature of 120 ° C, and start feeding, and the feeding amoun...
PUM
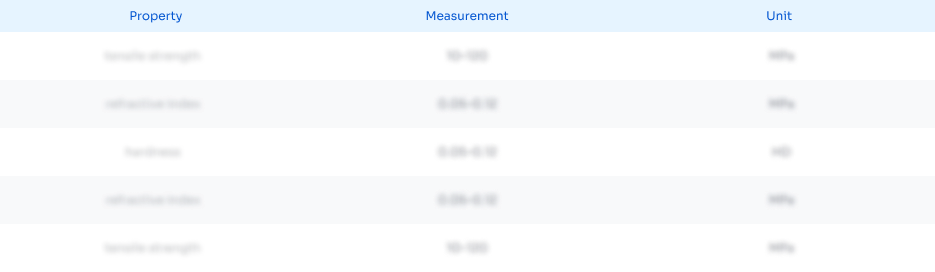
Abstract
Description
Claims
Application Information

- Generate Ideas
- Intellectual Property
- Life Sciences
- Materials
- Tech Scout
- Unparalleled Data Quality
- Higher Quality Content
- 60% Fewer Hallucinations
Browse by: Latest US Patents, China's latest patents, Technical Efficacy Thesaurus, Application Domain, Technology Topic, Popular Technical Reports.
© 2025 PatSnap. All rights reserved.Legal|Privacy policy|Modern Slavery Act Transparency Statement|Sitemap|About US| Contact US: help@patsnap.com