Method using selective laser sintering process to produce silicon carbide ceramic part
A technology of laser selective sintering and silicon carbide ceramics, applied in the field of rapid prototyping, can solve the problems of difficult control of sintering shrinkage and deformation, limited practical application and technical promotion, difficult to form large size and complex, and achieves small curing shrinkage and easy promotion. Application, good dimensional stability
- Summary
- Abstract
- Description
- Claims
- Application Information
AI Technical Summary
Problems solved by technology
Method used
Image
Examples
Embodiment 1
[0026] see figure 1 According to the first embodiment of the present invention, the method for preparing silicon carbide ceramic parts by laser selective sintering process includes the following steps:
[0027] (1) Weigh carbon powder, silicon carbide powder, adhesive and curing agent according to the predetermined mass ratio and pour them into the ball milling tank, then add an appropriate amount of balls into the ball milling tank, and ball mill at a speed of 135r / min 720min, that is, 12h, to obtain a uniformly dispersed binder-silicon carbide mixed powder.
[0028] In this embodiment, the mass ratio of the carbon powder to the silicon carbide powder is 4:96; the binder is a phenolic resin, and the mass of the phenolic resin is composed of the carbon powder and the silicon carbide powder. 25% of the mixed powder mass; the curing agent is hexamethylenetetramine, and the mass ratio of the hexamethylenetetramine to the phenolic resin is 7:100. Wherein, the D50 of the silicon ...
Embodiment 2
[0034] The method for preparing a silicon carbide ceramic part using a laser selective sintering process provided by the second embodiment of the present invention includes the following steps:
[0035] (1) Weigh carbon powder, silicon carbide powder, adhesive and curing agent according to the predetermined mass ratio and pour them into the ball milling tank, then add an appropriate amount of balls into the ball milling tank, and ball mill at a speed of 135r / min 720min, that is, 12h, to obtain a uniformly dispersed binder-silicon carbide mixed powder.
[0036] In this embodiment, the mass ratio of the carbon powder to the silicon carbide powder is 5:95; the binder is a phenolic resin, and the mass of the phenolic resin is composed of the carbon powder and the silicon carbide powder. 28% of the mass of the mixed powder; the curing agent is hexamethylenetetramine, and the mass ratio of the hexamethylenetetramine to the phenolic resin is 7:100. Wherein, the D50 of the silicon ca...
Embodiment 3
[0042] The method for preparing a silicon carbide ceramic part using a laser selective sintering process provided by the third embodiment of the present invention includes the following steps:
[0043] (1) Weigh carbon powder, silicon carbide powder, adhesive and curing agent according to the predetermined mass ratio and pour them into the ball milling tank, then add an appropriate amount of balls into the ball milling tank, and ball mill at a speed of 135r / min 720min, that is, 12h, to obtain a uniformly dispersed binder-silicon carbide mixed powder.
[0044] In this embodiment, the mass percentage of the carbon powder and the silicon carbide powder is 6:94; the binder is a phenolic resin, and the mass of the phenolic resin is composed of the carbon powder and the silicon carbide powder. 30% of the mass of the mixed powder; the curing agent is hexamethylenetetramine, and the mass ratio of the hexamethylenetetramine to the phenolic resin is 7:100. Wherein, the D50 of the silic...
PUM
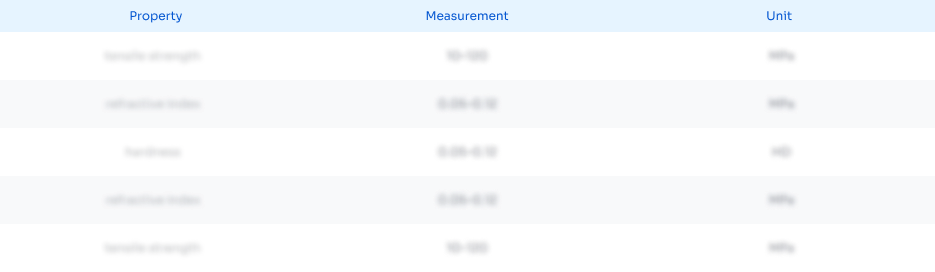
Abstract
Description
Claims
Application Information

- R&D Engineer
- R&D Manager
- IP Professional
- Industry Leading Data Capabilities
- Powerful AI technology
- Patent DNA Extraction
Browse by: Latest US Patents, China's latest patents, Technical Efficacy Thesaurus, Application Domain, Technology Topic, Popular Technical Reports.
© 2024 PatSnap. All rights reserved.Legal|Privacy policy|Modern Slavery Act Transparency Statement|Sitemap|About US| Contact US: help@patsnap.com