PET (polyester) release film
A release film and film layer technology, applied in the field of release film, can solve the problems that mechanical properties cannot meet the needs of the industry, poor heat sealing performance of PET release film, low thermal shrinkage rate, etc., to achieve good thermal stability and The effect of thermal shrinkage rate, more diversified functions, and simple synthesis method
- Summary
- Abstract
- Description
- Claims
- Application Information
AI Technical Summary
Problems solved by technology
Method used
Examples
Embodiment 1
[0027] A kind of PET release film, comprises film layer, and described film layer comprises following weight ratio raw material:
[0028] PET: 105 parts, PC: 11 parts, 2-ethyl methacrylate: 9.5 parts, polyurethane: 4.2 parts, polyimide: 2.58 parts, natural latex: 4.6 parts, calcium stearate: 2 parts, ethylene glycol Alcohol: 26 parts, silane coupling agent: 2.58 parts, antioxidant: 0.54 parts, light stabilizer: 0.6 parts, defoamer: 0.3 parts, thickener: 0.28 parts.
Embodiment 2
[0030] A kind of PET release film, comprises film layer, and described film layer comprises following weight ratio raw material:
[0031] PET: 95 parts, PC: 13 parts, 2-ethyl methacrylate: 10.5 parts, polyurethane: 4.5 parts, polyimide: 2.9 parts, natural latex: 3.4 parts, calcium stearate: 1.8 parts, ethylene glycol Alcohol: 20 parts, silane coupling agent: 2.3 parts, antioxidant: 0.35 parts, light stabilizer: 0.9 parts, defoamer: 0.15 parts, thickener: 0.36 parts.
Embodiment 3
[0033] A kind of PET release film, comprises film layer, and described film layer comprises following weight ratio raw material:
[0034] PET: 100 parts, PC: 10 parts, 2-ethyl methacrylate: 9 parts, polyurethane: 3 parts, polyimide: 2 parts, natural latex: 5.6 parts, calcium stearate: 1.5 parts, ethylene glycol Alcohol: 30 parts, silane coupling agent: 2.92 parts, antioxidant: 0.67 parts, light stabilizer: 0.15 parts, defoamer: 0.47 parts, thickener: 0.13 parts.
PUM
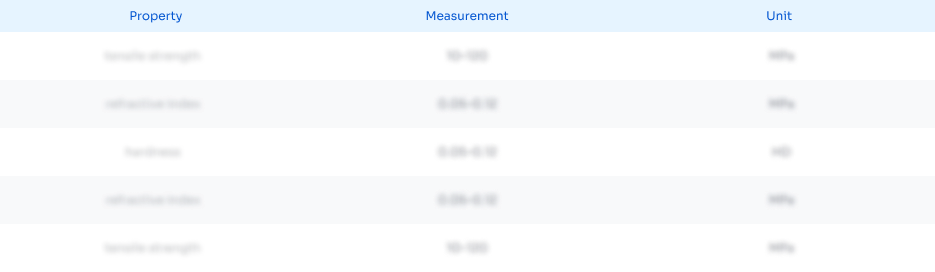
Abstract
Description
Claims
Application Information

- Generate Ideas
- Intellectual Property
- Life Sciences
- Materials
- Tech Scout
- Unparalleled Data Quality
- Higher Quality Content
- 60% Fewer Hallucinations
Browse by: Latest US Patents, China's latest patents, Technical Efficacy Thesaurus, Application Domain, Technology Topic, Popular Technical Reports.
© 2025 PatSnap. All rights reserved.Legal|Privacy policy|Modern Slavery Act Transparency Statement|Sitemap|About US| Contact US: help@patsnap.com