A kind of preparation method of composite hot-dip galvanized steel wire
A technology of hot-dip galvanizing and steel wire, applied in the field of steel wire, can solve the problems of uneven surface of galvanized layer, decreased corrosion resistance of chromic acid film, restricting the application of hot-dip galvanized steel wire, etc., to achieve smooth surface and ensure appearance and color requirements. , the effect of good application prospects
- Summary
- Abstract
- Description
- Claims
- Application Information
AI Technical Summary
Problems solved by technology
Method used
Image
Examples
Embodiment 1
[0026] (1) After the carbon steel high wire is quenched in a water bath, the first drawing is carried out, and then the steel wire after the first drawing is hot-dip galvanized through the hot-dip galvanizing treatment solution, and then the hot-dip galvanized steel wire is galvanized. After the second drawing, hot-dip galvanized steel wire can be obtained; water quenching liquid temperature: 95°C; furnace line temperature: 950°C; water line temperature: 650°C; dipping solution length: 2.4m; The zinc treatment solution also contains a plating flux; wherein, the flux is composed of: aluminum chloride 20g / L, zinc chloride 31g / L, potassium chloride 5g / L, sodium fluoride 6g / L, sodium bicarbonate 5g / L;
[0027] (2) After degreasing and washing the hot-dip galvanized steel wire obtained in step (1), adopt 2% silane coating agent (LG-209, Changzhou Lianggong Environmental Protection Technology Co., Ltd.) solution to impregnate and dry to make the hot-dip galvanized steel wire A sil...
Embodiment 2
[0030] (1) After the carbon steel high wire is quenched in a water bath, the first drawing is carried out, and then the steel wire after the first drawing is hot-dip galvanized through the hot-dip galvanizing treatment solution, and then the hot-dip galvanized steel wire is galvanized. After the second drawing, hot-dip galvanized steel wire is obtained; water quenching liquid temperature: 95°C; furnace line temperature: 950°C; water line temperature: 64°C; dipping solution length: 3.2m; steel wire immersion depth: 15mm; The zinc treatment solution also contains a plating flux; wherein, the flux is composed of: aluminum chloride 25g / L, zinc chloride 35g / L, potassium chloride 6g / L, sodium fluoride 8g / L, sodium bicarbonate 5g / L;
[0031] (2) After degreasing and washing the hot-dip galvanized steel wire obtained in step (1), adopt 2% silane coating agent (LG-209, Changzhou Lianggong Environmental Protection Technology Co., Ltd.) solution to impregnate and dry to make the hot-dip...
PUM
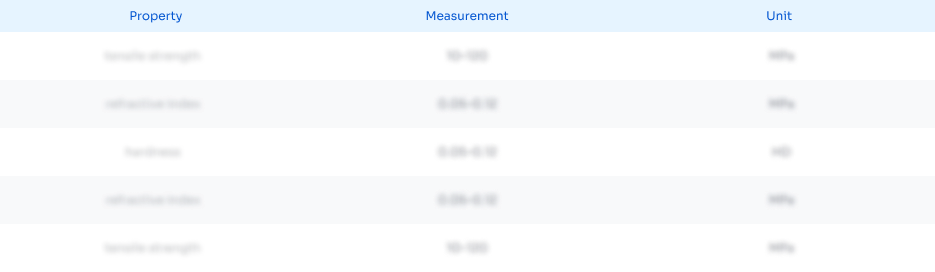
Abstract
Description
Claims
Application Information

- R&D Engineer
- R&D Manager
- IP Professional
- Industry Leading Data Capabilities
- Powerful AI technology
- Patent DNA Extraction
Browse by: Latest US Patents, China's latest patents, Technical Efficacy Thesaurus, Application Domain, Technology Topic, Popular Technical Reports.
© 2024 PatSnap. All rights reserved.Legal|Privacy policy|Modern Slavery Act Transparency Statement|Sitemap|About US| Contact US: help@patsnap.com