A kind of method for preparing sodium hypochlorite
A sodium hypochlorite and chlorine gas technology, applied in hypochlorous acid, hypochlorite, chemical instruments and methods, etc., can solve the problems of increasing production costs and tail gas treatment costs, reducing effective chlorine content, increasing sodium hypochlorite, etc., to reduce tail gas Disposal cost, strong anti-oxidation ability, effect of inhibiting decomposition
- Summary
- Abstract
- Description
- Claims
- Application Information
AI Technical Summary
Problems solved by technology
Method used
Image
Examples
Embodiment 1
[0035] Step1: According to parts by weight, weigh 3 parts of silicon nitride, 4 parts of sodium silicate and 1000 parts of sodium chloride;
[0036] Step2: Put the weighed silicon nitride, sodium silicate and sodium chloride in a double-helix mixer, mix them evenly, and press them into shape;
[0037] Step3: Under nitrogen protection, control the temperature at 650°C for sintering;
[0038] Step4: Grind after cooling and forming, and pass through a 200-mesh sieve to obtain the product.
Embodiment 2
[0040] Step1: According to parts by weight, weigh 4 parts of silicon nitride, 2 parts of sodium silicate and 1500 parts of sodium chloride;
[0041] Step2: Put the weighed silicon nitride, sodium silicate and sodium chloride in a double-helix mixer, mix them evenly, and press them into shape;
[0042] Step3: Under nitrogen protection, control the temperature at 675°C for sintering;
[0043] Step4: Grind after cooling and forming, and pass through a 200-mesh sieve to obtain the product.
Embodiment 3
[0045] Step1: According to parts by weight, weigh 6 parts of silicon nitride, 3 parts of sodium silicate and 2000 parts of sodium chloride;
[0046] Step2: Put the weighed silicon nitride, sodium silicate and sodium chloride in a double-helix mixer, mix them evenly, and press them into shape;
[0047] Step3: Under nitrogen protection, control the temperature at 700°C for sintering;
[0048] Step4: Grind after cooling and forming, and pass through a 200-mesh sieve to obtain the product.
PUM
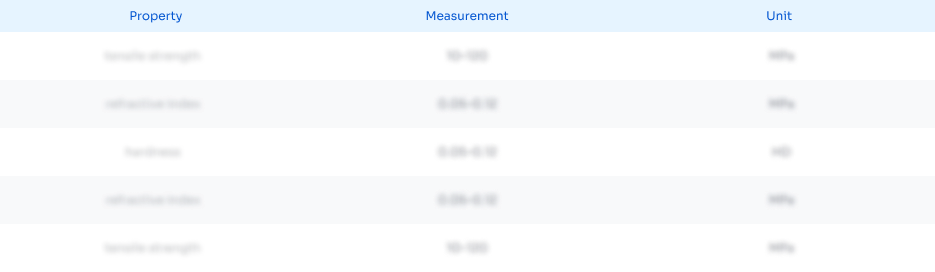
Abstract
Description
Claims
Application Information

- R&D Engineer
- R&D Manager
- IP Professional
- Industry Leading Data Capabilities
- Powerful AI technology
- Patent DNA Extraction
Browse by: Latest US Patents, China's latest patents, Technical Efficacy Thesaurus, Application Domain, Technology Topic, Popular Technical Reports.
© 2024 PatSnap. All rights reserved.Legal|Privacy policy|Modern Slavery Act Transparency Statement|Sitemap|About US| Contact US: help@patsnap.com