Environment-friendly treatment process for blow-in flue gas of zinc sulfide concentrate fluidized roaster
A technology of fluidized roasting and zinc sulfide concentrate, which is applied in gas treatment, climate change adaptation, climate sustainability, etc., can solve problems such as air pollution, achieve the effect of reducing air pollution and avoiding equipment damage
- Summary
- Abstract
- Description
- Claims
- Application Information
AI Technical Summary
Problems solved by technology
Method used
Image
Examples
Embodiment 1
[0026] The environmental protection treatment process for flue gas from the start-up of a zinc sulfide concentrate fluidized roaster is characterized in that it includes the following steps:
[0027] (1) Furnace start-up flue gas is sent to the purification process from the bypass smoke pipe through the furnace start-up fan to avoid the electric dust collector; the air volume of the furnace start-up fan is 12000m 3 / h~50580m 3 / h, flue gas dust content ~ 0.5g / m 3 , the flue gas contains SO 2 Amount ~ 0.25g / m 3 , Flue gas temperature 200 ~ 350 ℃.
[0028] (2) The flue gas from the furnace is purified and sprayed by the first-level high-efficiency scrubber and the packing cooling tower; the flow rate of the first-level high-efficiency scrubber and the packing cooling tower is 200m 3 / h~350m 3 / h.
[0029] (3) Furnace start-up flue gas avoids the electric demister and dry suction and conversion process and enters the tail gas treatment device from the bypass flue pipe.
[...
Embodiment 2
[0032] The environmental protection treatment process for flue gas from the start-up of a zinc sulfide concentrate fluidized roaster is characterized in that it includes the following steps:
[0033] (1) Furnace start-up flue gas is sent to the purification process from the bypass smoke pipe through the furnace start-up fan to avoid the electric dust collector; the air volume of the furnace start-up fan is 30000m 3 / h~150000m 3 / h, flue gas dust content ~ 0.5g / m 3 , the flue gas contains SO 2 Amount ~ 0.15g / m 3 , Flue gas temperature 200 ~ 350 ℃.
[0034] (2) The flue gas from the furnace is purified and sprayed by the first-level high-efficiency scrubber and the packing cooling tower; the flow rate of the first-level high-efficiency scrubber and the packing cooling tower is 400m 3 / h~550m 3 / h.
[0035] (3) Furnace start-up flue gas avoids the electric demister and dry suction and conversion process and enters the tail gas treatment device from the bypass flue pipe.
...
PUM
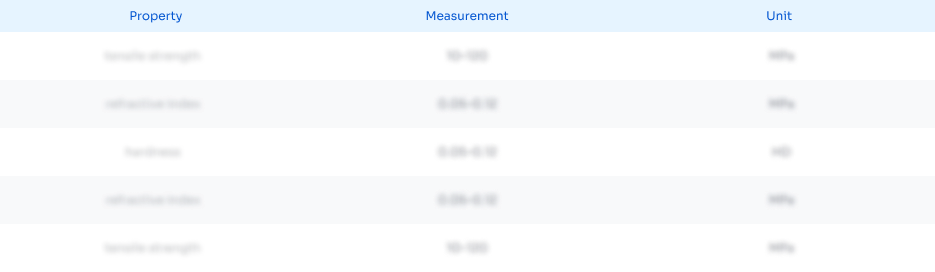
Abstract
Description
Claims
Application Information

- Generate Ideas
- Intellectual Property
- Life Sciences
- Materials
- Tech Scout
- Unparalleled Data Quality
- Higher Quality Content
- 60% Fewer Hallucinations
Browse by: Latest US Patents, China's latest patents, Technical Efficacy Thesaurus, Application Domain, Technology Topic, Popular Technical Reports.
© 2025 PatSnap. All rights reserved.Legal|Privacy policy|Modern Slavery Act Transparency Statement|Sitemap|About US| Contact US: help@patsnap.com