A molding method of composite material with lightning protection function
A composite material and lightning protection technology, applied in the direction of coating, etc., can solve the problems of increasing the manufacturing cost of composite material structure, increasing the weight of composite material structure, and easy corrosion of metal materials, so as to avoid corrosion and weak adhesion, Meet the lightning protection requirements and reduce the effect of lightning damage
- Summary
- Abstract
- Description
- Claims
- Application Information
AI Technical Summary
Problems solved by technology
Method used
Image
Examples
preparation example Construction
[0015] 1) Preparation of a resin film dispersed with conductive nano particles. Mix and disperse the nano-conductive particles and the resin containing the solvent under a high-speed mixer for 2-3 hours, then dissolve the film-forming agent in the dispersed nano-conductive particles and resin mixture, add a high-temperature curing agent and mix. Finally, the obtained resin system is poured on an iron plate at 90-120° C., and cast to form a resin film containing dispersed nano conductive particles.
[0016] 2) The fiber preform is shaped. First, the resin film and fiber cloth are cut according to the size of the mold, and then the cut fiber cloth is laid along the surface of the mold, and then the resin film is covered on it, and finally, the surrounding area of the preform is sealed with a sealant.
[0017] 3) Forming the fiber preform. According to the resin film infiltration process, a microporous filter membrane is laid on the preform, a vacuum diversion system is const...
Embodiment 1
[0029] In this embodiment, taking the preparation of an aircraft cabin door as an example, multi-walled carbon nanotubes are used to improve the surface conductivity of the carbon fiber reinforced cyanate ester composite material, so as to reduce the damage caused by lightning to the aircraft cabin door.
[0030] The specific method is,
[0031] 1) Preparation of dispersed multi-walled carbon nanotube resin film. Add 0.5 parts of multi-walled carbon nanotubes modified by hexadecylamine to 300 parts of dimethyl phthalate, mix and disperse for 3 hours under a high-speed mixer, and then add 100 parts of N,N'- (4,4'-methylenediphenyl), ultrasonically dispersed at room temperature for 30 minutes and then stirred at high speed for 2 hours.
[0032] The dispersed multi-walled carbon nanotubes and resin mixture were stirred at 180° C. for 12 hours, and the solvent was removed by evaporation. Then, raise the material temperature to 135°C, add 86 parts of 2,2'-diallyl bisphenol A, sti...
Embodiment 2
[0037]In this embodiment, taking the preparation of the UAV wing as an example, nano-silver is used to improve the surface conductivity of the glass fiber reinforced epoxy resin composite material, so as to reduce the damage caused by lightning to the UAV wing.
[0038] The specific method is,
[0039] 1) Preparation of resin film dispersed with nano-silver. Add 1 part of nano-silver to 300 parts of acetone, stir at high speed, then add 100 parts of novolac epoxy resin F-51, ultrasonically disperse at room temperature for 30 minutes, and then mix and disperse under a high-speed mixer for 2 hours 1 Hour. The dispersed multi-walled carbon nanotubes and epoxy resin mixture were stirred at 90° C. for 12 hours, and the solvent was removed by evaporation. Then, raise the material temperature to 190°C, add 5 parts of film-forming agent polyethersulfone, stir to dissolve it in the resin, then lower the temperature to 120°C, add 30 parts of high-temperature curing agent diaminodiphen...
PUM
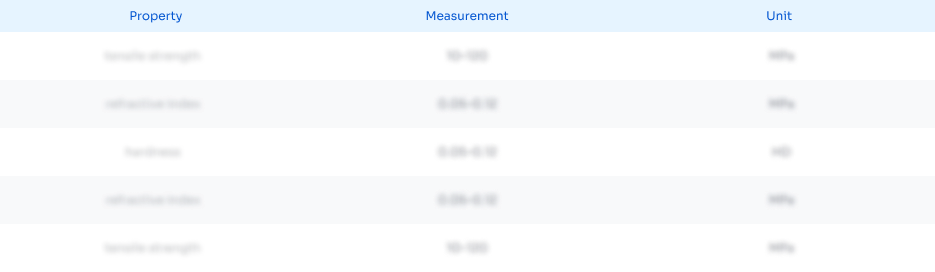
Abstract
Description
Claims
Application Information

- R&D
- Intellectual Property
- Life Sciences
- Materials
- Tech Scout
- Unparalleled Data Quality
- Higher Quality Content
- 60% Fewer Hallucinations
Browse by: Latest US Patents, China's latest patents, Technical Efficacy Thesaurus, Application Domain, Technology Topic, Popular Technical Reports.
© 2025 PatSnap. All rights reserved.Legal|Privacy policy|Modern Slavery Act Transparency Statement|Sitemap|About US| Contact US: help@patsnap.com