Separating and recovering method for W and V in waste SCR denitration catalyst
A technology of denitration catalyst and recovery method, which is applied in the field of recovery and separation of metal tungsten and vanadium in waste SCR denitration catalyst, which can solve the problems of inability to achieve efficient metal separation, cumbersome operation process, and low metal leaching rate
- Summary
- Abstract
- Description
- Claims
- Application Information
AI Technical Summary
Problems solved by technology
Method used
Image
Examples
Embodiment 1
[0058] a Take a waste SCR denitrification catalyst (the main component is V 2 o 5 -WO 3 / TiO 2 , the specific components are shown in Table 1), the deactivated SCR denitrification catalyst is blown with clean and dry compressed air to remove the fly ash deposited on the surface of the catalyst, wherein the working pressure of the compressed air is 0.5MPa, and the gas flow rate is 0.5m 3 / s, the purge time is 10min. Grind the catalyst into powder in a mortar, and then sieve it with a standard sieve of not less than 100 meshes, and then dry the catalyst powder at 105°C for 2 hours.
[0059] B takes by weighing the catalyst powder 5g that dries in step a, after cooling, adds Na to wherein 2 CO 3 solid, Na 2 CO 3 The mass ratio of the mixture to the catalyst is 0.5, and after being fully mixed, it is placed in a muffle furnace, and fired at 800° C. for 3 hours to obtain a sintered block.
[0060]c Use dilute sulfuric acid solution with a concentration of 2% (v / v) to leach ...
Embodiment 2
[0062] a Take a waste SCR denitrification catalyst (the main component is V 2 o 5 -WO 3 / TiO 2 , the specific components are shown in Table 1), the deactivated SCR denitrification catalyst is blown with clean and dry compressed air to remove the fly ash deposited on the surface of the catalyst, wherein the working pressure of the compressed air is 0.5MPa, and the gas flow rate is 0.5m 3 / s, the purge time is 10min. Grind the catalyst into powder in a mortar, and then sieve it with a standard sieve of not less than 100 meshes, and then dry the catalyst powder at 105°C for 2 hours.
[0063] B takes by weighing the catalyst powder 5g that dries in step a, after cooling, adds Na to wherein 2 CO 3 solid, Na 2 CO 3 The mass ratio of the mixture to the catalyst is 1.2. After being fully mixed, it is placed in a muffle furnace, and fired at 800° C. for 5 hours to obtain a sintered block.
[0064] c Use a dilute sulfuric acid solution with a concentration of 10% (v / v) to leach ...
Embodiment 3
[0066] a Take a waste SCR denitrification catalyst (the main component is V 2 o 5 -WO 3 / TiO 2 , the specific components are shown in Table 1), the deactivated SCR denitrification catalyst is blown with clean and dry compressed air to remove the fly ash deposited on the surface of the catalyst, wherein the working pressure of the compressed air is 0.5MPa, and the gas flow rate is 0.5m 3 / s, the purge time is 10min. Grind the catalyst into powder in a mortar, and then sieve it with a standard sieve of not less than 100 meshes, and then dry the catalyst powder at 105°C for 2 hours.
[0067] B takes by weighing the catalyst powder 5g that dries in step a, after cooling, adds Na to wherein 2 CO 3 solid, Na 2 CO 3 The mass ratio of the mixture to the catalyst is 1.2, and after being fully mixed, it is placed in a muffle furnace, and fired at 800° C. for 3 hours to obtain a sintered block.
[0068] c Use dilute sulfuric acid solution with a concentration of 2% (v / v) to leach...
PUM
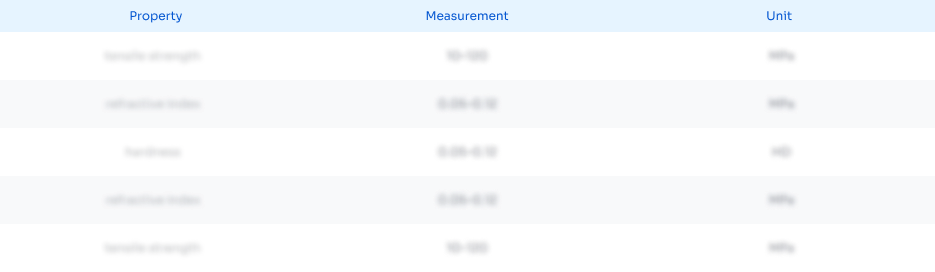
Abstract
Description
Claims
Application Information

- Generate Ideas
- Intellectual Property
- Life Sciences
- Materials
- Tech Scout
- Unparalleled Data Quality
- Higher Quality Content
- 60% Fewer Hallucinations
Browse by: Latest US Patents, China's latest patents, Technical Efficacy Thesaurus, Application Domain, Technology Topic, Popular Technical Reports.
© 2025 PatSnap. All rights reserved.Legal|Privacy policy|Modern Slavery Act Transparency Statement|Sitemap|About US| Contact US: help@patsnap.com