Resin material and preparation method thereof
A technology of resin material and matrix resin, applied in the field of resin material and its preparation, can solve the problems of complex production process, high comprehensive cost and high energy consumption, and achieve the effects of improving compatibility, improving production efficiency and improving impact resistance.
- Summary
- Abstract
- Description
- Claims
- Application Information
AI Technical Summary
Problems solved by technology
Method used
Image
Examples
preparation example Construction
[0063] The present invention also provides a method for preparing the aforementioned resin material, which includes the following steps:
[0064] The base resin, toughening agent, compatibilizer, and coloring masterbatch are placed at 80°C to 120°C and dried for 4 to 6 hours.
[0065] Each raw material is added to a high-speed mixer, and mixed for 1 min to 5 min to obtain a mixture.
[0066] The mixture is melted and pelletized by a twin-screw extrusion pelletizing unit; wherein the heating temperature is 180°C to 250°C, the die temperature is 195°C to 210°C, and the screw speed of the main engine is 400r / min to 550r / min, the feeding speed is 40r / min~60r / min.
[0067] The drying process of the matrix resin, toughening agent, compatibilizer, and coloring masterbatch can make the matrix resin, toughening agent, compatibilizing agent, and coloring masterbatch obtain excellent performance that is more suitable for mixing, and ensure the subsequent mixing process. The uniformity and qual...
PUM
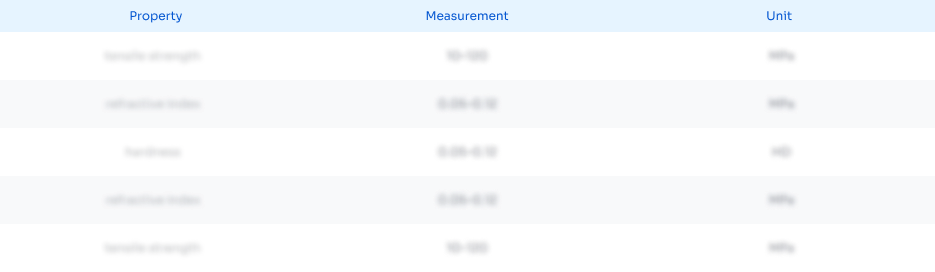
Abstract
Description
Claims
Application Information

- Generate Ideas
- Intellectual Property
- Life Sciences
- Materials
- Tech Scout
- Unparalleled Data Quality
- Higher Quality Content
- 60% Fewer Hallucinations
Browse by: Latest US Patents, China's latest patents, Technical Efficacy Thesaurus, Application Domain, Technology Topic, Popular Technical Reports.
© 2025 PatSnap. All rights reserved.Legal|Privacy policy|Modern Slavery Act Transparency Statement|Sitemap|About US| Contact US: help@patsnap.com