Alloy material for chip processing system of marine drilling platform and preparation method of alloy material
A technology for offshore drilling platforms and alloy materials, which is applied in the field of alloy materials and preparations for cuttings processing systems on offshore drilling platforms, and can solve problems such as backward high-end offshore drilling equipment and energy reserves that cannot meet the needs of world economic development.
- Summary
- Abstract
- Description
- Claims
- Application Information
AI Technical Summary
Problems solved by technology
Method used
Image
Examples
Embodiment 1
[0043] Raw material components:
[0044] C: 0.05%, Mn: 1.0%, Si: 1.0%, S: 0.03%, P: 0.03%, Cr: 14.50%, Ni: 5.70%, Mo: 0.90%, Cu: 1.50%, Ir: 0.50%, Mg: 0.50%, Al: 2.0%, V: 0.90%, W: 0.90%, Pb: 1.40%, Nb: 0.90%, Sn: 0.35%, Zn: 0.90%, Ho: 0.15%, Lu: 0.45%, , and the rest is Fe.
[0045] Prepared by:
[0046] Step S01, Fe, Mn, Cr, Ni, Mo, Cu, Ir, Mg, Al, W, Pb, Nb, Sn, Zn, Ho, Lu elemental substances to be smelted are added to the vacuum of the water-cooled copper crucible according to the material composition ratio. Indoor, vacuumize and melt at a sintering temperature of 980°C;
[0047] Step S02, adding C, Si, S, P, V simple substances according to the material composition ratio under the condition of metal melting, stirring evenly, and keeping warm for 46 minutes;
[0048] Step S03, under the condition of helium pressurization of 47Mpa, cool to 700°C at a cooling rate of 44°C / min, hold for 46min, then raise the temperature to 750°C at a heating rate of 44°C / min and hold for...
Embodiment 2
[0050] Raw material components:
[0051] C: 0.05%, Mn: 1.0%, Si: 0.60%, S: 0.03%, P: 0.03%, Cr: 14.0%, Ni: 5.0%, Mo: 0.50%, Cu: 1.25%, Ir: 0.30%, Mg: 0.40%, Al: 1.90%, V: 0.60%, W: 0.60%, Pb: 1.30%, Nb: 0.60%, Sn: 0.30%, Zn: 0.60%, Lu: 0.20%, and the rest is Fe.
[0052] Prepared by:
[0053] Step S01, adding Fe, Mn, Cr, Ni, Mo, Cu, Ir, Mg, Al, W, Pb, Nb, Sn, Zn, Lu elemental substances to be smelted into the vacuum chamber of the water-cooled copper crucible according to the material composition ratio, Vacuumize and melt at a sintering temperature of 950°C;
[0054] Step S02, adding C, Si, S, P, V simple substances according to the material composition ratio under the condition of metal melting, stirring evenly, and keeping warm for 40 minutes;
[0055] Step S03, under the condition of helium pressurization of 30Mpa, cool to 700°C at a cooling rate of 30°C / min, hold for 30min, then raise the temperature to 750°C at a heating rate of 30°C / min and hold for 30min for annealin...
Embodiment 3
[0057] Raw material components:
[0058] C: 0.10%, Mn: 2.0%, Si: 1.50%, S: 0.04%, P: 0.04%, Cr: 16.0%, Ni: 7.0%, Mo: 1.0%, Cu: 1.75%, Ir: 0.60%, Mg: 1.0%, Al: 2.20%, V: 1.50%, W: 1.50%, Pb: 1.70%, Nb: 1.50%, Sn: 0.40%, Zn: 1.50%, Lu: 0.45%, Ho: 0.45%, The rest is Fe.
[0059] Prepared by:
[0060] Step S01, adding the Fe, Mn, Cr, Ni, Mo, Cu, Ir, Mg, Al, W, Pb, Nb, Sn, Zn, Lu, Ho elemental substances to be smelted into the vacuum of the water-cooled copper crucible according to the material composition ratio. Vacuumize the room and melt at a sintering temperature of 1000°C;
[0061] Step S02, adding C, Si, S, P, V simple substances according to the material composition ratio under the condition of metal melting, stirring evenly, and keeping warm for 50 minutes;
[0062] Step S03, under the condition of argon pressurization of 50Mpa, cool to 700°C at a cooling rate of 50°C / min, hold for 50min, then raise the temperature to 750°C at a heating rate of 50°C / min and hold for 50m...
PUM
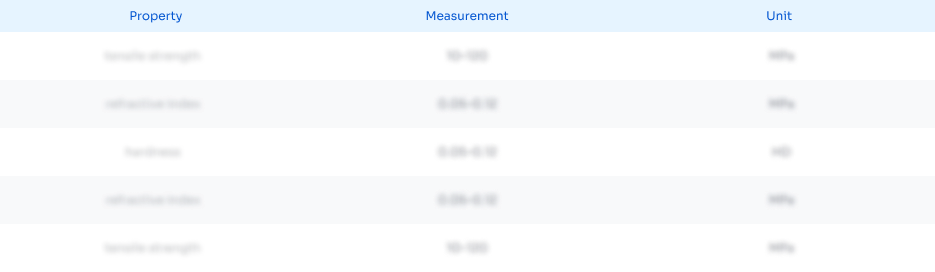
Abstract
Description
Claims
Application Information

- R&D Engineer
- R&D Manager
- IP Professional
- Industry Leading Data Capabilities
- Powerful AI technology
- Patent DNA Extraction
Browse by: Latest US Patents, China's latest patents, Technical Efficacy Thesaurus, Application Domain, Technology Topic, Popular Technical Reports.
© 2024 PatSnap. All rights reserved.Legal|Privacy policy|Modern Slavery Act Transparency Statement|Sitemap|About US| Contact US: help@patsnap.com