Cable material for electric thermal insulation, insulation and flame retardance and preparation method thereof
A cable and electric technology, which is applied in the field of electrical insulation and flame-retardant cable materials and its preparation, can solve the problems of suffocation, fueling fire, loss, etc., and achieve the effect of simple preparation process and good corrosion resistance
- Summary
- Abstract
- Description
- Claims
- Application Information
AI Technical Summary
Problems solved by technology
Method used
Examples
preparation example Construction
[0024] A method for preparing a power heat insulation and flame retardant cable material, comprising the steps of:
[0025] S1. Weigh 32-38 parts of PVC polyvinyl chloride, 22-30 parts of magnesium hydroxide, 11-14 parts of phthalate, 11-18 parts of ethylene-propylene rubber, 16-20 parts of mixed resin, and melamine cyanuric acid according to parts by weight. 24-28 parts of salt, 1-2 parts of stearic acid, 6-9 parts of dioctyl phthalate, 3-7 parts of polyethylene glycol, 2-4 parts of azobisisobutyronitrile, 6 parts of fatty wax -8 parts, 3-8 parts of dicumyl peroxide, 11-13 parts of maleic anhydride grafted polyethylene, 1-2 parts of zinc pyrithione, and 1-2 parts of cyclohexanedimethanol are poured into ultrasonic high-speed dispersion In the machine, ultrasonic high-speed dispersion is carried out to obtain mixed solution A;
[0026] S2. Add 20-35 parts of diatomaceous earth and 11-14 parts of glass fiber to the mixed solution A obtained in step S1, and perform ultrasonic h...
Embodiment 1
[0031]S1. Weigh 36 parts of PVC polyvinyl chloride, 28 parts of magnesium hydroxide, 12 parts of phthalate, 16 parts of ethylene-propylene rubber, 17 parts of mixed resin, 26 parts of melamine cyanurate, 2 parts of stearic acid, Dioctyl phthalate 7 parts, polyethylene glycol 5 parts, azobisisobutyronitrile 3 parts, aliphatic acid 7 parts, dicumyl peroxide 5 parts, maleic anhydride grafted polyethylene 12 parts , 1 part of zinc pyrithione, and 1 part of cyclohexanedimethanol are poured into an ultrasonic high-speed disperser for ultrasonic high-speed dispersion to obtain a mixed solution A;
[0032] S2. Add 27 parts of diatomaceous earth and 13 parts of glass fiber to the mixed solution A obtained in step S1, and perform ultrasonic high-speed dispersion to obtain mixed solution B;
[0033] S3. Add 7 parts of compatibilizer, 3 parts of anti-aging agent, 7 parts of flame retardant, 3 parts of plasticizer and 4 parts of vulcanizing agent to the mixed solution B obtained in step S2...
Embodiment 2
[0037] S1. Weigh 38 parts of PVC polyvinyl chloride, 30 parts of magnesium hydroxide, 14 parts of phthalate, 18 parts of ethylene-propylene rubber, 20 parts of mixed resin, 28 parts of melamine cyanurate, 2 parts of stearic acid, Dioctyl phthalate 9 parts, polyethylene glycol 7 parts, azobisisobutyronitrile 4 parts, aliphatic acid 8 parts, dicumyl peroxide 8 parts, maleic anhydride grafted polyethylene 13 parts , 2 parts of zinc pyrithione, and 2 parts of cyclohexanedimethanol are poured into an ultrasonic high-speed disperser for ultrasonic high-speed dispersion to obtain a mixed solution A;
[0038] S2. Add 35 parts of diatomaceous earth and 14 parts of glass fiber to the mixed solution A obtained in step S1, and then perform ultrasonic high-speed dispersion to obtain mixed solution B;
[0039] S3. Add 8 parts of compatibilizer, 4 parts of anti-aging agent, 8 parts of flame retardant, 4 parts of plasticizer and 5 parts of vulcanizing agent to the mixed solution B obtained in...
PUM
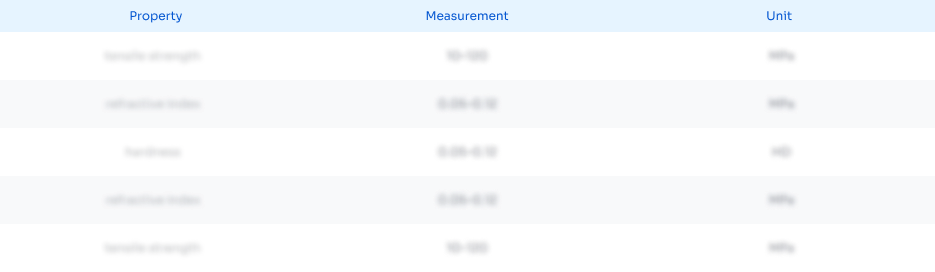
Abstract
Description
Claims
Application Information

- Generate Ideas
- Intellectual Property
- Life Sciences
- Materials
- Tech Scout
- Unparalleled Data Quality
- Higher Quality Content
- 60% Fewer Hallucinations
Browse by: Latest US Patents, China's latest patents, Technical Efficacy Thesaurus, Application Domain, Technology Topic, Popular Technical Reports.
© 2025 PatSnap. All rights reserved.Legal|Privacy policy|Modern Slavery Act Transparency Statement|Sitemap|About US| Contact US: help@patsnap.com