Nozzle and manufacturing method thereof
A manufacturing method and channel technology, applied in the combustion method, burner, combustion type and other directions, can solve the problems of limited service life of the burner, the flame shape cannot be effectively controlled, and the structure is complex, and achieves the reduction of the amount of iron oxide scale in the billet forging, comprehensive Good combustion performance and the effect of overcoming excessive local temperature
- Summary
- Abstract
- Description
- Claims
- Application Information
AI Technical Summary
Problems solved by technology
Method used
Image
Examples
Embodiment 1
[0036] combine Figure 1~3 ( figure 1 for figure 2The view along the C direction), the burner of this embodiment includes a burner body 1 and a primary air channel 2, a secondary air channel 3 and a natural gas channel 4 located in the burner body 1, and the primary air channel 2 starts from the primary air The direction from the inlet 21 to the primary air outlet 22 is an equal cross-section channel section and a gradually widening channel section (specifically, the gradually widening channel section is a bell mouth hollow structure), and there are at least three secondary air channels 3 distributed around the circumference of the primary air channel 2 ( Three or more secondary air passages 3 have the effect of refining and splitting the secondary air), and the natural gas outlet 42 of the natural gas passage 4 communicates with the gradually widening passage section. Wherein, the included angle between the natural gas channel 4 and the central axis of the above-mentioned ...
Embodiment 2
[0050] The structure of the burner of this embodiment is basically the same as that of Embodiment 1, except that three secondary air passages 3 are distributed along the left middle, right middle and lower middle sides of the primary air passage 2, and three The included angle between the secondary air channel 3 and the central axis of the equal-section channel section is 4°, the included angle between the natural gas channel 4 and the central axis of the equal-section channel section is 35°, and the two sides on the axial section of the gradually widening channel section The included angle is 40°. The pipe diameter of the channel section with constant cross section is The pipe diameter of the secondary air channel 3 is The pipe diameter of natural gas channel 4 is
Embodiment 3
[0052] The burner of this embodiment, its structure is basically the same as that of Embodiment 1, the difference is that: four secondary air passages 3 are symmetrically distributed on the four sides of the primary air passage 2; four secondary air passages 3 and The angle between the central axis of the channel section with constant cross section is 6°, the angle between the natural gas channel 4 and the central axis of the channel section with equal cross section is 45°, and the angle between the two sides on the axial section of the gradually widening channel section is 50° . The pipe diameter of the channel section with constant cross section is The pipe diameter of the secondary air channel 3 is The pipe diameter of natural gas channel 4 is
PUM
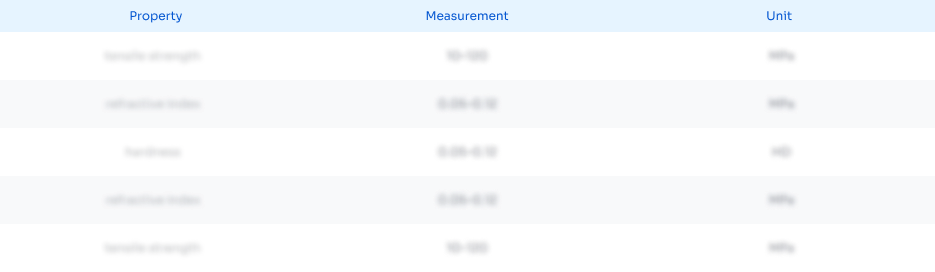
Abstract
Description
Claims
Application Information

- R&D
- Intellectual Property
- Life Sciences
- Materials
- Tech Scout
- Unparalleled Data Quality
- Higher Quality Content
- 60% Fewer Hallucinations
Browse by: Latest US Patents, China's latest patents, Technical Efficacy Thesaurus, Application Domain, Technology Topic, Popular Technical Reports.
© 2025 PatSnap. All rights reserved.Legal|Privacy policy|Modern Slavery Act Transparency Statement|Sitemap|About US| Contact US: help@patsnap.com