Metal additive for aluminum alloy smelting and using method thereof
A metal additive and aluminum alloy technology, which is applied in the field of aluminum and aluminum alloy production, can solve the problems of low yield rate, large burning loss of metal elements, uneven metal composition of aluminum alloy, etc.
- Summary
- Abstract
- Description
- Claims
- Application Information
AI Technical Summary
Problems solved by technology
Method used
Examples
Embodiment 1
[0022] manganese additive
[0023] Proportion: metal manganese powder: 80%, titanium hydride powder: 1%, aluminum powder 4%, potassium fluoroaluminate 15%. The purity of manganese powder is 99.5%, the particle size is 80 mesh, and the purity of aluminum powder is greater than 95%.
[0024] Process: Mix the powder after batching, and then press into a specific mold.
[0025] How to use: When the temperature of the metal aluminum liquid reaches 680°C, add the pressed manganese additive into the aluminum liquid, let it rest for 5 minutes, then raise the temperature to 740°C, and then let it rest for 15 minutes. The actual yield of manganese is 99.6%.
Embodiment 2
[0027] Titanium Additives
[0028] Proportion: metal titanium powder: 80%, titanium hydride powder: 0.5%, aluminum powder 2%, potassium fluoroaluminate 13.5%. The purity of titanium powder is 99.7%, the particle size is 80 mesh, and the purity of aluminum powder is greater than 95%.
[0029] Process: Mix the powder after batching, and then press into a specific mold.
[0030] How to use: When the temperature of the metal aluminum liquid reaches 670°C, add the pressed titanium additive into the aluminum liquid, let it stand still for 5 minutes, then raise the temperature to 730°C, and then stand still for 20 minutes. The actual yield of titanium is 99.4%.
Embodiment 3
[0032] iron additive
[0033] Ratio: metal iron powder: 75%, titanium hydride powder: 1.5%, aluminum powder 6%, potassium fluoroaluminate 13.5%. The purity of iron powder is 99.3%, the particle size is 80 mesh, and the purity of aluminum powder is more than 95%.
[0034] Process: Mix the powder after batching, and then press into a specific mold.
[0035] How to use: When the temperature of the metal aluminum liquid reaches 700°C, add the pressed iron additive into the aluminum liquid, let it rest for 5 minutes, then raise the temperature to 750°C, and let it stand for another 19 minutes. The actual yield of iron is 99.5%.
PUM
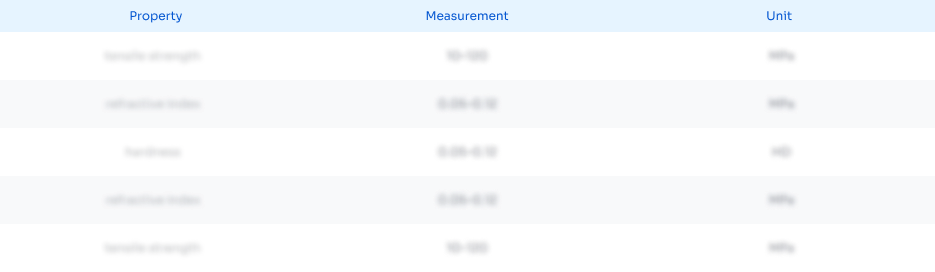
Abstract
Description
Claims
Application Information

- Generate Ideas
- Intellectual Property
- Life Sciences
- Materials
- Tech Scout
- Unparalleled Data Quality
- Higher Quality Content
- 60% Fewer Hallucinations
Browse by: Latest US Patents, China's latest patents, Technical Efficacy Thesaurus, Application Domain, Technology Topic, Popular Technical Reports.
© 2025 PatSnap. All rights reserved.Legal|Privacy policy|Modern Slavery Act Transparency Statement|Sitemap|About US| Contact US: help@patsnap.com