Co-extrusion polyethylene film and film blowing forming process
A technology of co-extrusion polyethylene and molding process, which is applied in the chemical industry, can solve the problems of limited use range, difficult printing of polyethylene materials, etc., and achieve the effect of avoiding equipment safety and eliminating static electricity
- Summary
- Abstract
- Description
- Claims
- Application Information
AI Technical Summary
Problems solved by technology
Method used
Examples
Embodiment 1
[0027] In an embodiment of the present invention, a co-extruded polyethylene film includes an outer layer, a middle layer and an inner layer; the raw materials of the outer layer include 22% of low-density polyethylene and 78% of medium-density polyethylene according to mass percentage; The raw materials include 50% of high-density polyethylene and 50% of low-density polyethylene; the raw materials of the inner layer include 55% of high molecular material, 28% of low-density polyethylene, 16.5% of linear low-density polyethylene and 0.5% of additives according to mass percentage. The mass ratio of outer layer: middle layer: inner layer is 3:5:1. Among them, low-density polyethylene can be LDPE2420H, LDPETN00, LDPETX00, etc.; medium-density polyethylene can be MDPE5401, MDPE7520NT, etc.; high-density polyethylene can be HDPE5000S, HDPE8008, etc.; linear low-density polyethylene can be LLDPE 7042, LLDPE1002, LLDPE920NT, LLDPE218W, etc.; the polymer material is a thermoplastic el...
Embodiment 2
[0029] In an embodiment of the present invention, a co-extruded polyethylene film includes an outer layer, a middle layer and an inner layer; the raw materials of the outer layer include 70% of low-density polyethylene and 30% of medium-density polyethylene according to mass percentage; The raw materials include 70% of high-density polyethylene and 30% of low-density polyethylene; the raw materials of the inner layer include 30% of high molecular material, 40% of low-density polyethylene, 29.7% of linear low-density polyethylene and 0.3% of additives according to mass percentage. The mass ratio of outer layer: middle layer: inner layer is 5:3:1. Among them, low-density polyethylene can be LDPE2420H, LDPETN00, LDPETX00, etc.; medium-density polyethylene can be MDPE5401, MDPE7520NT, etc.; high-density polyethylene can be HDPE5000S, HDPE8008, etc.; linear low-density polyethylene can be LLDPE 7042, LLDPE1002, LLDPE920NT, LLDPE218W, etc.; the polymer material is a thermoplastic el...
Embodiment 3
[0031] In an embodiment of the present invention, a co-extruded polyethylene film includes an outer layer, a middle layer and an inner layer; the raw materials of the outer layer include 50% of low-density polyethylene and 50% of medium-density polyethylene according to mass percentage; The raw materials include 65% of high-density polyethylene and 35% of low-density polyethylene; the raw materials of the inner layer include 45% of high molecular material, 35% of low-density polyethylene, 19.8% of linear low-density polyethylene and 0.2% of additives according to the mass percentage. The mass ratio of outer layer: middle layer: inner layer is 2:8:1. Among them, low-density polyethylene can be LDPE2420H, LDPETN00, LDPETX00, etc.; medium-density polyethylene can be MDPE5401, MDPE7520NT, etc.; high-density polyethylene can be HDPE5000S, HDPE8008, etc.; linear low-density polyethylene can be LLDPE 7042, LLDPE1002, LLDPE920NT, LLDPE218W, etc.; the polymer material is a thermoplasti...
PUM
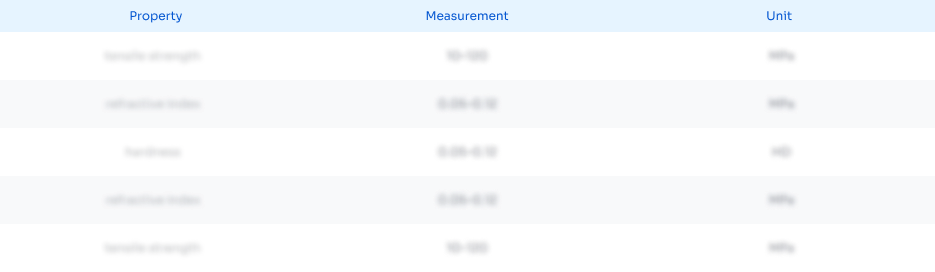
Abstract
Description
Claims
Application Information

- R&D
- Intellectual Property
- Life Sciences
- Materials
- Tech Scout
- Unparalleled Data Quality
- Higher Quality Content
- 60% Fewer Hallucinations
Browse by: Latest US Patents, China's latest patents, Technical Efficacy Thesaurus, Application Domain, Technology Topic, Popular Technical Reports.
© 2025 PatSnap. All rights reserved.Legal|Privacy policy|Modern Slavery Act Transparency Statement|Sitemap|About US| Contact US: help@patsnap.com