Method for preparing qualified microalloy iron powder through high-hydrogen-loss high-carbon primary reduced iron powder
A technology of micro-alloyed iron powder and reduced iron powder, applied in metal processing equipment, transportation and packaging, etc., can solve the problems of high resource dependence, strong stability, hydrogen loss and low carbon content, and achieve the expansion of rich resources, The effect of suppressing the increase of hydrogen loss and reducing the overall manufacturing cost
- Summary
- Abstract
- Description
- Claims
- Application Information
AI Technical Summary
Problems solved by technology
Method used
Examples
Embodiment 1
[0026] Mix low-grade vanadium-titanium magnetite with ordinary anthracite at a mass ratio of 55.65:13, then add industrial salt and grind and separate after conventional catalytic reduction at 1060°C for 33 hours to obtain primary reduced iron with high hydrogen loss and high carbon powder (grinding separation process is: crushing→grinding magnetic separation (three repetitions)→dehydration→drying→classification→high hydrogen loss and high carbon primary iron powder).
[0027] Among them, the chemical composition of low-grade vanadium-titanium magnetite is: TFe 55.65%, SiO 2 4.45%, Al 2 o 3 3.73%, TiO 2 6.86%, V 2 o 5 0.79%, S 0.120%, FeO 24.23%; the chemical composition of ordinary anthracite is: Ash 14.80%, V9.20%, S 0.80%, fixed C content 77.36%, fineness 60 mesh; the chemical composition of industrial salt is: NaCl 99.3 %, KCl0.025%, MgCl 2 0.025%, CaCl 0.025%, CaSO 4 0.25%, SiO 2 0.025%.
[0028] The main components of the obtained primary reduced iron pow...
Embodiment 2
[0034] Mix low-grade vanadium-titanium magnetite with ordinary anthracite at a mass ratio of 55:12, then add industrial salt and grind and separate after conventional catalytic reduction at 1040°C for 36 hours to obtain primary reduced iron with high hydrogen loss and high carbon powder (grinding separation process is: crushing→grinding magnetic separation (three repetitions)→dehydration→drying→classification→high hydrogen loss and high carbon primary iron powder).
[0035] Among them, the chemical composition of low-grade vanadium-titanium magnetite is: TFe 54.93%, SiO 2 4.87%, Al 2 o 3 3.79%, TiO 2 7.03%, V 2 o 5 0.76%, S 0.126%, FeO 22.63%; the chemical composition of ordinary anthracite is: Ash 15.67%, V9.55%, S 0.86%, fixed C content 75.88%, fineness 60 mesh; the chemical composition of industrial salt is: NaCl 99.2 %, KCl0.028%, MgCl 2 0.022%, CaCl 0.031%, CaSO 4 0.27%, SiO 2 0.020%.
[0036] The main components of the obtained primary reduced iron powder...
Embodiment 3
[0042] Mix low-grade vanadium-titanium magnetite with ordinary anthracite at a mass ratio of 57:15, then add industrial salt and grind and separate after conventional catalytic reduction at 1080°C for 32 hours to obtain primary reduced iron with high hydrogen loss and high carbon powder (grinding separation process is: crushing→grinding magnetic separation (three repetitions)→dehydration→drying→classification→high hydrogen loss and high carbon primary iron powder).
[0043] Among them, the chemical composition of low-grade vanadium-titanium magnetite is: TFe 55.93%, SiO 2 4.47%, Al 2 o 3 3.39%, TiO 2 6.63%, V 2 o 5 0.71%, S 0.116%, FeO 23.85%; chemical composition of ordinary anthracite: Ash 15.25%, V8.98%, S 0.86, fixed C content 76.01%, fineness 60 mesh; industrial salt chemical composition: NaCl 99.32% , KCl0.033%, MgCl 2 0.021%, CaCl 0.029%, CaSO 4 0.23%, SiO 2 0.022%.
[0044] The main components of the obtained primary reduced iron powder with high hydrog...
PUM
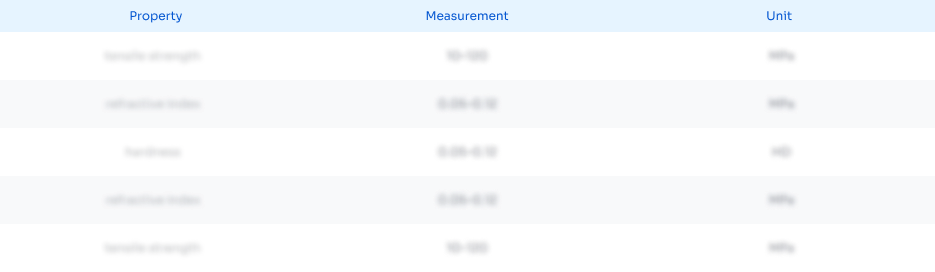
Abstract
Description
Claims
Application Information

- R&D
- Intellectual Property
- Life Sciences
- Materials
- Tech Scout
- Unparalleled Data Quality
- Higher Quality Content
- 60% Fewer Hallucinations
Browse by: Latest US Patents, China's latest patents, Technical Efficacy Thesaurus, Application Domain, Technology Topic, Popular Technical Reports.
© 2025 PatSnap. All rights reserved.Legal|Privacy policy|Modern Slavery Act Transparency Statement|Sitemap|About US| Contact US: help@patsnap.com