Easily molded toughened ceramic section for cement ball mill and preparation method thereof
A technology of toughening ceramics and cement balls, applied in the field of cement processing, can solve the problems of low hardness, insufficient strength, and poor high temperature resistance of the grinding body, and achieve the effects of high hardness, good bonding force, and long replacement cycle.
- Summary
- Abstract
- Description
- Claims
- Application Information
AI Technical Summary
Problems solved by technology
Method used
Image
Examples
Embodiment 1
[0032] The easy-to-form toughened ceramic segment for the cement ball mill contains 92% of alumina, 0.5% of ferric oxide, 0.8% of kaolin, 2.5% of tungsten carbide, 2% of titanium dioxide, 1% of titanium carbide, and 1.2% of tantalum carbide by weight percentage. Prepared as follows:
[0033] (a) Batching: get all ingredients by weight percentage; configure PVA solution simultaneously, proportioning is PVA:water=8:100;
[0034] (b) Ball milling:
[0035] (b1) Primary grinding: Add the ingredients calculated in step (a) to the primary grinding equipment, and add ball stones and water (the primary grinding balls can be Φ30-Φ50mm 92-high alumina isostatic balls, the same below) , the ratio is material: ball: water=1:2.5:0.7, stop grinding to slurry fineness D90≤8 micron, cross 40 mesh sieves and go out grinding;
[0036] (b2) Fine grinding: Add the slurry obtained in step (b1) into the fine grinding equipment, and add ball stones and water (fine grinding ball stones can be 92-hi...
Embodiment 2
[0045] The easy-to-form toughened ceramic segment for the cement ball mill contains 95% of alumina, 0.5% of ferric oxide, 0.8% of kaolin, 1% of tungsten carbide, 0.5% of titanium dioxide, 1% of titanium carbide, and 1.2% of tantalum carbide by weight percentage. Prepared as follows:
[0046] (a) Batching: get all ingredients by weight percentage; configure PVA solution simultaneously, proportioning is PVA:water=7:100;
[0047] (b) Ball milling:
[0048] (b1) Primary grinding: Add the ingredients calculated in step (a) to the primary grinding equipment, and add ball stones and water in a ratio of material: ball: water = 1:2.5:0.75, until the slurry fineness D90≤8 Micron stop grinding, pass through a 40-mesh sieve for grinding;
[0049] (b2) Fine grinding: Add the slurry obtained in step (b1) to the fine grinding equipment, and add ball stones and water in a ratio of material: ball: water = 1:3:0.75, until the fineness of the slurry is D50≤1.5 microns 、Stop grinding after D90...
Embodiment 3
[0058] The easy-to-form toughened ceramic segment for the cement ball mill contains 92% of alumina, 2% of ferric oxide, 1.7% of kaolin, 2% of tungsten carbide, 0.5% of titanium dioxide, 0.8% of titanium carbide, and 1% of tantalum carbide by weight percentage. Prepared as follows:
[0059] (a) Batching: get all ingredients by weight percentage; configure PVA solution simultaneously, proportioning is PVA:water=10:100;
[0060] (b) Ball milling:
[0061] (b1) Primary grinding: Add the ingredients calculated in step (a) to the primary grinding equipment, and add ball stones and water in a ratio of material: ball: water = 1:2.5:0.72, until the slurry fineness D90≤8 Micron stop grinding, pass through a 40-mesh sieve for grinding;
[0062] (b2) fine grinding: add the slurry obtained in step (b1) into the fine grinding equipment, and add ball stones and water in a ratio of material: ball: water = 1: 2.5: 0.75, until the fineness of the slurry is D50≤1.5 microns 、Stop grinding afte...
PUM
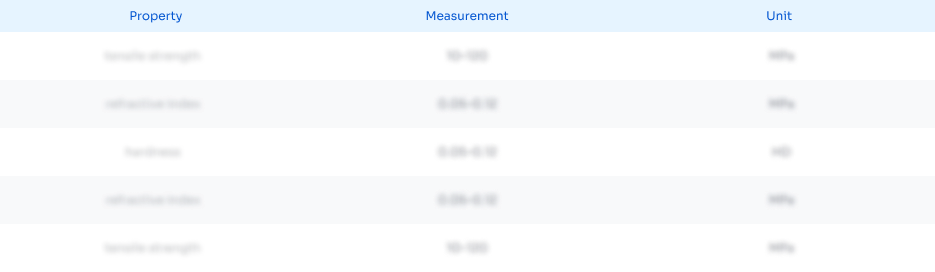
Abstract
Description
Claims
Application Information

- R&D
- Intellectual Property
- Life Sciences
- Materials
- Tech Scout
- Unparalleled Data Quality
- Higher Quality Content
- 60% Fewer Hallucinations
Browse by: Latest US Patents, China's latest patents, Technical Efficacy Thesaurus, Application Domain, Technology Topic, Popular Technical Reports.
© 2025 PatSnap. All rights reserved.Legal|Privacy policy|Modern Slavery Act Transparency Statement|Sitemap|About US| Contact US: help@patsnap.com