Polyurethane foam base adhesive tape
A technology of polyurethane and foam, which is applied in the direction of adhesives, film/sheet adhesives, etc., can solve the problems of insufficient shock resistance, large thickness, and insufficient strength, and achieve nucleation of cells, thin thickness, and elasticity. and good toughness
- Summary
- Abstract
- Description
- Claims
- Application Information
AI Technical Summary
Problems solved by technology
Method used
Image
Examples
Embodiment 1
[0045] Mix 100 parts of polyester polyol and 11.5 parts of HDI in N 2 Heating and reacting under ambient conditions for 1.5 hours, the reaction temperature is 70°C, then cooling down to 50°C, adding 8 parts of chain extender diethylene glycol, keeping the reaction for 3 hours, then adding 1.0 parts of light stabilizer UV-329 and 5 parts of medium Porous Nano TiO 2 , stir evenly to obtain a polyurethane prepolymer, add 5 parts of cross-linking agent HDI trimer to the polyurethane prepolymer, stir evenly, and cure at 100°C for 20 minutes to obtain a polyurethane base material, the isocyanate index of the polyurethane base material is 3.5 ;
[0046] The polyurethane base material is made into a polyurethane film or sheet by a common method;
[0047] Put the polyurethane film or sheet in a high-pressure reactor, first use supercritical CO 2 Purge the system with fluid, drain the air, seal the autoclave, raise the temperature of the system to 110°C, and inject CO 2 The fluid co...
Embodiment 2
[0050] Mix 100 parts of polyester polyol and 19.3 parts of HDI in N 2 Heating and reacting under ambient conditions for 2.0 hours, the reaction temperature is 78°C, then cooling down to 60°C, adding 10 parts of chain extender glycerene propylene ether, keeping it warm for 3.5 hours, then adding 1.8 parts of light stabilizer antioxidant 1010 and 8 parts of silane Coupling agent modified mesoporous nano-TiO 2 , stir evenly to obtain a polyurethane prepolymer, add 8 parts of cross-linking agent HDI trimer to the polyurethane prepolymer, stir evenly, and cure at 110°C for 25 minutes to obtain a polyurethane base material, the isocyanate index of the polyurethane base material is 4.2 ;
[0051] The polyurethane base material is made into a polyurethane film or sheet by a common method;
[0052] Put the polyurethane film or sheet in a high-pressure reactor, first use supercritical CO 2 Purge the system with fluid, drain the air, seal the autoclave, raise the temperature of the sy...
Embodiment 3
[0055] Mix 100 parts of polyester polyol and 28.3 parts of HDI in N 2 Heat the reaction for 2.5 hours under ambient conditions, the reaction temperature is 85°C, then cool down to 65°C, add 12 parts of chain extender diethanolamine, keep it warm for 4 hours, then add 2.5 parts of light stabilizer GW-540 and 5-11 parts of titanate Coupling agent modified mesoporous nano-TiO 2 , stir evenly to obtain a polyurethane prepolymer, add 13 parts of cross-linking agent HDI trimer to the polyurethane prepolymer, stir evenly, and cure at 115°C for 30 minutes to obtain a polyurethane base material, the isocyanate index of the polyurethane base material is 4.6 ;
[0056] The polyurethane base material is made into a polyurethane film or sheet by a common method;
[0057] Put the polyurethane film or sheet in a high-pressure reactor, first use supercritical CO 2 Purge the system with fluid, drain the air, seal the autoclave and raise the temperature of the system to 120°C, inject CO 2 T...
PUM
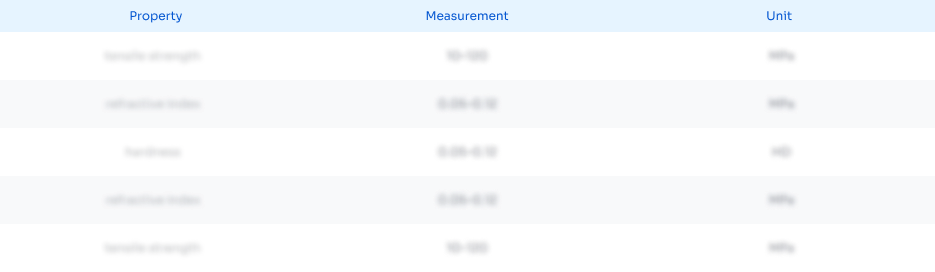
Abstract
Description
Claims
Application Information

- R&D
- Intellectual Property
- Life Sciences
- Materials
- Tech Scout
- Unparalleled Data Quality
- Higher Quality Content
- 60% Fewer Hallucinations
Browse by: Latest US Patents, China's latest patents, Technical Efficacy Thesaurus, Application Domain, Technology Topic, Popular Technical Reports.
© 2025 PatSnap. All rights reserved.Legal|Privacy policy|Modern Slavery Act Transparency Statement|Sitemap|About US| Contact US: help@patsnap.com