Method for refining bismuth from bismuth oxide slags
A technology of bismuth oxide slag and rough bismuth, which is applied in the field of refined bismuth, can solve the problems that zinc cannot be recycled and reused, the direct yield of bismuth is low, and the cost of smelting is high, so as to save wet pretreatment, reduce the amount of nitric acid used, simplify Effect of Copper Removal Process
- Summary
- Abstract
- Description
- Claims
- Application Information
AI Technical Summary
Problems solved by technology
Method used
Image
Examples
Embodiment 1
[0059] The method for refining bismuth from bismuth oxide slag comprises the following steps:
[0060] a. Reduction smelting
[0061] 30kg of carbon particles with a carbon content of > 90% in the anode particles and 1T bismuth oxide slag are reduced and smelted in a converter at a melting temperature of 700°C. The carbon particles can also be replaced by coke particles with a carbon content of > 90% in the anode particles or Other reducing agents, slag for recovery of lead;
[0062] b. Copper removal by melting
[0063] The crude bismuth obtained by reduction smelting is subjected to smelting and copper removal. First, the temperature of the crude bismuth is raised to 650°C, stirred evenly, and then the temperature is slowly lowered to 550°C. The copper removal slag is used to recover copper, and this step is repeated until the melt contains less than 3% copper; When the copper content in bismuth is 40-50%, first add sulfur to remove copper, and then carry out smelting to r...
Embodiment 2-10
[0075] The differences between Examples 2-10 and Example 1 are shown in Table 3, and the rest of the reaction conditions are the same as in Example 1.
[0076] table 3
[0077]
PUM
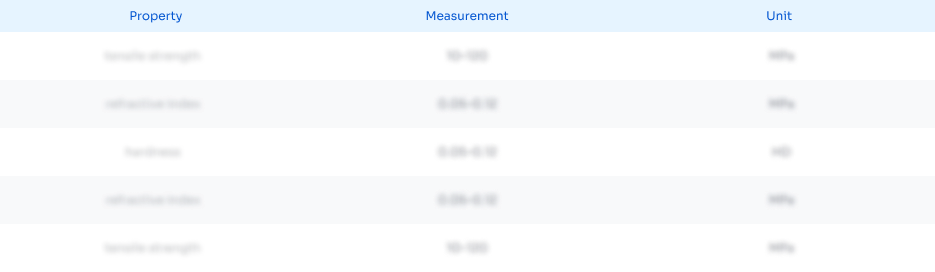
Abstract
Description
Claims
Application Information

- R&D
- Intellectual Property
- Life Sciences
- Materials
- Tech Scout
- Unparalleled Data Quality
- Higher Quality Content
- 60% Fewer Hallucinations
Browse by: Latest US Patents, China's latest patents, Technical Efficacy Thesaurus, Application Domain, Technology Topic, Popular Technical Reports.
© 2025 PatSnap. All rights reserved.Legal|Privacy policy|Modern Slavery Act Transparency Statement|Sitemap|About US| Contact US: help@patsnap.com