Preparation process for producing damping sheet by virtue of waste rubber
A preparation process, technology of waste rubber, applied in the field of preparation process of using waste rubber to produce damping sheet, can solve the problems of high performance, etc., achieve rich hand feeling elasticity, improve initial tack and holding force, and reduce wear rate Effect
- Summary
- Abstract
- Description
- Claims
- Application Information
AI Technical Summary
Problems solved by technology
Method used
Examples
Embodiment 1
[0026] First, add 45 parts by weight of waste rubber to the pulverizer for pulverization, then transfer the pulverized material to a desulfurization kettle for high-temperature desulfurization, and filter it, and then transfer the filtered material to a kneader for kneading and stirring , the stirring speed is 50 revolutions / s;
[0027] Next, in the kneader after the aforementioned stirring, adding parts by weight is 40 parts of modified graphene nanofillers, 23 parts of N-isopropylmaleimide-methyl methacrylate, tetrafluoroethylene-perfluoroalkyl 31 parts of vinyl ether copolymerized fibers, 22 parts of polymethyl methacrylate, continue to stir for 2 hours, and then add 9 parts by weight of isobutylene, 8 parts by weight of white carbon black and 4 parts by weight of carbon black in the kneader. Black, after kneading and stirring for 5.5 hours, the material was transferred to the stirring device; and the stirring speed was 50 rpm / s;
[0028] Add 46 parts by weight of iron pow...
Embodiment 2
[0031] First, add 45 parts by weight of waste rubber to the pulverizer for pulverization, then transfer the pulverized material to a desulfurization kettle for high-temperature desulfurization, and filter it, and then transfer the filtered material to a kneader for kneading and stirring , the stirring speed is 49 revolutions / s;
[0032] Next, in the kneader after the aforementioned stirring, adding parts by weight is 40 parts of modified graphene nanofillers, 23 parts of N-isopropylmaleimide-methyl methacrylate, tetrafluoroethylene-perfluoroalkyl 31 parts of vinyl ether copolymerized fibers, 22 parts of polymethyl methacrylate, continue to stir for 1 hour, then add 9 parts by weight of isobutylene, 8 parts by weight of white carbon black and 4 parts by weight of carbon black in the kneader. Black, after kneading and stirring for 6 hours, the material was transferred to the stirring device; and the stirring speed was 49 rpm / s;
[0033] Add 46 parts by weight of iron powder, 46...
Embodiment 3
[0036] First, add 45 parts by weight of waste rubber to the pulverizer for pulverization, then transfer the pulverized material to a desulfurization kettle for high-temperature desulfurization, and filter it, and then transfer the filtered material to a kneader for kneading and stirring , the stirring speed is 48 rpm / s;
[0037] Next in the kneader after the aforementioned stirring, add the modified graphene nano-filler that the weight part is 40 parts, continue to stir for 2 hours, add the isobutylene that the weight part is 9, the white carbon black that the weight part is 8 in the kneader again in the kneader and The carbon black of 4 parts by weight, after kneading and stirring for 5 hours, the material is transferred to the stirring device; and the stirring speed is 48 revolutions / s;
[0038]Add 46 parts by weight of iron powder, 46 parts by weight of aluminum powder, 1.0 part by weight of antifungal agent and 5 parts by weight of pottery clay to the stirring device again...
PUM
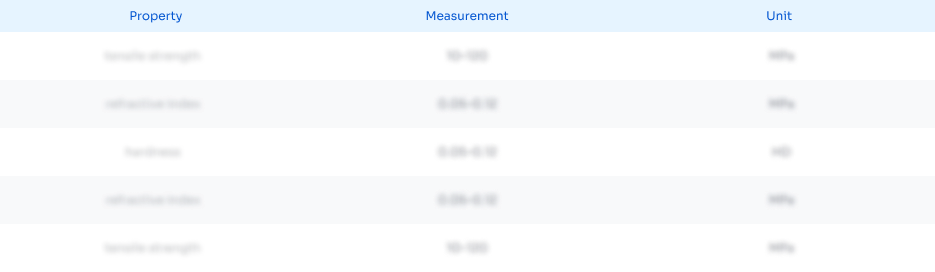
Abstract
Description
Claims
Application Information

- R&D Engineer
- R&D Manager
- IP Professional
- Industry Leading Data Capabilities
- Powerful AI technology
- Patent DNA Extraction
Browse by: Latest US Patents, China's latest patents, Technical Efficacy Thesaurus, Application Domain, Technology Topic, Popular Technical Reports.
© 2024 PatSnap. All rights reserved.Legal|Privacy policy|Modern Slavery Act Transparency Statement|Sitemap|About US| Contact US: help@patsnap.com