High-anti-slippery abrasion-resistant material for shoes and preparation method thereof
A wear-resistant material and anti-slip technology, which is applied in the field of shoes, can solve problems such as increasing the difficulty of production, and achieve the effects of enhancing mechanical properties, improving wear resistance and anti-wet skid performance
- Summary
- Abstract
- Description
- Claims
- Application Information
AI Technical Summary
Problems solved by technology
Method used
Image
Examples
Embodiment 1
[0022] 30 parts of natural rubber, 20 parts of styrene-butadiene rubber, 25 parts of cis-butadiene rubber and 25 parts by weight of brominated butyl rubber are sent into an open mill to carry out open milling. Mixed rubber material after milling and 8 parts by weight of zinc oxide, 1 part by weight of tetramethylthiuram monosulfide, 1 part by weight of N-phenyl-1-naphthylamine, 15 parts by weight of rubber oil, 0.5 parts by weight of stearin Acid, 13 parts by weight of white carbon black and 27 parts by weight of nano-calcium carbonate are put into a banbury mixer for banbury mixing together, the temperature of the banbury mixer is 125°C, and the material is discharged after banbury mixing for 4 minutes; the above-mentioned mixed glue is discharged into a designated mold and cooled for 24 Hours; After cooling, add 1 part by weight of sulfur, 4.5 parts by weight of silicon carbide and 4 parts by weight of silicone peroxide coupling agent, and send it into a vulcanizing machine f...
Embodiment 2
[0024] First 40 parts of natural rubber, 25 parts of styrene-butadiene rubber, 20 parts of cis-butadiene rubber and 23 parts by weight of chlorinated butyl rubber are prepared and sent into the mill for milling. The roller distance of the mill is 1mm, and the thin pass is 10 times; Finally, the mixed rubber material after milling is mixed with 4 parts by weight of zinc carbonate, 3 parts by weight of dibenzothiazole disulfide, 3 parts by weight of N-phenyl-N'-isopropyl-p-phenylenediamine, 20 parts by weight of rubber oil , 1 part by weight of stearic acid, 17 parts by weight of white carbon black and 23 parts by weight of nanometer calcium carbonate are put into banbury mixer banbury together, and banbury mixer temperature is 110 ℃, discharge after banbury mixing 4 minutes; Above-mentioned mixed glue is discharged into In the designated mold, cool for 24 hours; after cooling, add 2 parts by weight of sulfur, 3.5 parts by weight of silicon carbide and 3 parts by weight of α-func...
Embodiment 3
[0026] 30 parts of natural rubber, 40 parts of styrene-butadiene rubber, 25 parts of cis-butadiene rubber and 15 parts by weight of iodized butyl rubber are sent into an open mill to carry out open milling. Finally, mix the mixed rubber material after milling with 3 parts by weight of titanium dioxide, 2 parts by weight of N, N'-bicyclohexyl-2-benzothiazole sulfenamide, 2 parts by weight of 2-mercaptobenzimidazole, 15 parts by weight Part rubber oil, 1.5 parts by weight of stearic acid, 20 parts by weight of white carbon black and 20 parts by weight of nano-calcium carbonate are dropped into banbury mixer banbury together, and banbury mixer temperature is 100 ℃, discharge after banbury mixing 5 minutes; Above-mentioned mixing The rubber is discharged into the designated mold and cooled for 24 hours; after cooling, add 2 parts by weight of sulfur, 3 parts by weight of silicon carbide and 2 parts by weight of long-chain alkylsilane coupling agent, and send it to a vulcanizer for ...
PUM
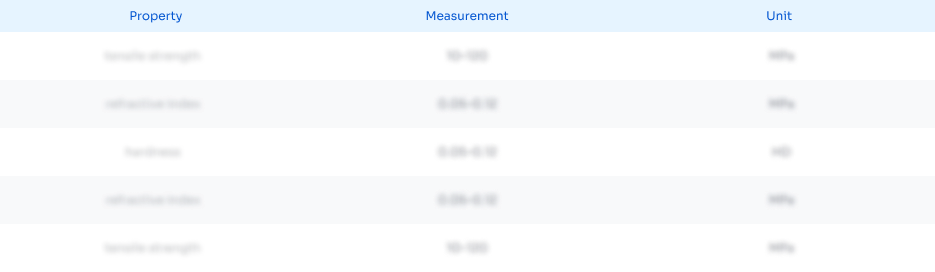
Abstract
Description
Claims
Application Information

- Generate Ideas
- Intellectual Property
- Life Sciences
- Materials
- Tech Scout
- Unparalleled Data Quality
- Higher Quality Content
- 60% Fewer Hallucinations
Browse by: Latest US Patents, China's latest patents, Technical Efficacy Thesaurus, Application Domain, Technology Topic, Popular Technical Reports.
© 2025 PatSnap. All rights reserved.Legal|Privacy policy|Modern Slavery Act Transparency Statement|Sitemap|About US| Contact US: help@patsnap.com