Method for reducing and reusing sulfur-bearing waste water of coking unit
A technology for coking equipment and sewage, which is applied in the field of reduction and reuse of sulfur-containing sewage in coking equipment. It can solve problems such as water analysis and optimization of equipment, large production of sulfur-containing sewage, and great potential for water saving and emission reduction, so as to reduce sulfur The amount of sewage, the realization of economic and environmental benefits, and the effect of increasing the amount
- Summary
- Abstract
- Description
- Claims
- Application Information
AI Technical Summary
Problems solved by technology
Method used
Image
Examples
Embodiment 1
[0048] The coking unit of a refinery has a design processing capacity of 2.4 million t / a. After water and drainage analysis, the following optimization measures can be taken:
[0049] 1) By adjusting the steam injection in the heating furnace tube, the sealing gas of the ball valve and the small blowing steam, the total amount of sulfur-containing sewage at the top of the fractionation tower is reduced from 10t / h to 7t / h;
[0050] 2) Absorbing and stabilizing the sulfur-containing sewage from the liquid separation tank of the stabilizing tower and reusing it for water injection at the top of the fractionating tower;
[0051] 3) Purified water replaces the blown steam cold coke. The device needs to blow steam twice a day, each time for 2.5 hours, and the steam blowing volume is about 20t / h, and about 45t of 1.0MPa steam is needed to process one tower of coke; if purified water is used instead, only about 6t is needed to treat one tower of coke, which can save The 1.0MPa steam ...
Embodiment 2
[0056] The 1.4 million t / a coking unit of a refinery takes the following process adjustment measures:
[0057] 1) The steam injection rate of the heating furnace is reduced from the original 2.4t / h to 1.8t / h;
[0058] 2) The steam consumption of small blowing steam is reduced from 6t / h to 2.5t / h, and the steam consumption of large blowing steam is reduced from 20t / h to 11t / h, saving 50t of steam per day;
[0059] 3) Cancellation of water injection at the top of the fractionation tower;
[0060] 4) Use purified water after stripping instead of demineralized water to inject water into the outlet of the coking gas-enriched compressor (before air cooling), and the water injection rate is 1.5t / h;
[0061] Through the above optimization and adjustment, the device can save 23,000 tons of steam annually, reduce the generation of sulfur-containing sewage by 23,000 tons, and increase the reuse of purified water by 13,000 tons.
Embodiment 3
[0063] The 1.6 million t / a coking unit of a refinery, through the analysis of the water and drainage of the unit, took the following optimization measures:
[0064] 1) The steam injection rate of the heating furnace tube is reduced from 3t / h to 2t / h;
[0065] 2) The amount of stripping steam in the fractionator wax oil stripper is reduced from 1t / h to 0.5t / h;
[0066] 3) The sulfur-containing sewage in the liquid separator tank of the absorption stabilization system is directly cascaded and used for water injection at the top of the fractionation tower;
[0067] 4) Use purified water after stripping instead of desalinated water to inject water into the outlet of the coking gas-enriched compressor (before air cooling), saving softened water and reducing the production of sulfur-containing sewage by 2t / h;
[0068] 5) The small steam blowing is reduced from 6t / h to 4t / h, and the large steam blowing is reduced from 20t / h to 12t / h;
[0069] 6) The original steam consumption of th...
PUM
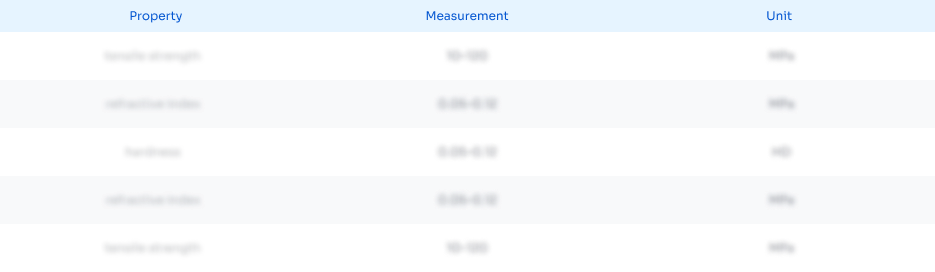
Abstract
Description
Claims
Application Information

- R&D
- Intellectual Property
- Life Sciences
- Materials
- Tech Scout
- Unparalleled Data Quality
- Higher Quality Content
- 60% Fewer Hallucinations
Browse by: Latest US Patents, China's latest patents, Technical Efficacy Thesaurus, Application Domain, Technology Topic, Popular Technical Reports.
© 2025 PatSnap. All rights reserved.Legal|Privacy policy|Modern Slavery Act Transparency Statement|Sitemap|About US| Contact US: help@patsnap.com