Method and device for extracting lithium from lapidolite by chloridizing roasting method
A technology for lepidolite and lithium extraction, applied in the field of metallurgy, can solve the problems of insufficient chlorination of lithium concentrate, low lithium recovery rate, low roasting temperature, etc., so as to increase the amount of water treatment and wastewater discharge, and the utilization rate of equipment. Low, high energy consumption effect
- Summary
- Abstract
- Description
- Claims
- Application Information
AI Technical Summary
Problems solved by technology
Method used
Image
Examples
Embodiment 1
[0025] Will Li 2Lepidolite, calcium chloride, sodium hydroxide and composite binder with O content of 4% are mixed in a mass ratio of 1:0.8:0.05:0.08 to make green pellets of 5-12 mm in size, wherein the composite binder is A mixture of sodium humate, quicklime, sodium carbonate, and potassium carbonate. The above-mentioned green pellets were calcined at 1100°C for 4 hours, and after the furnace gas was cooled, the dust containing a mixture of lithium chloride, potassium chloride, sodium chloride, rubidium chloride and cesium chloride was collected. The above-mentioned soot is leached with a solution containing sodium carbonate and potassium carbonate. The sum of the contents of sodium carbonate and potassium carbonate is greater than 120% of the theoretical amount required to convert lithium in the soot into lithium carbonate. Potassium, sodium, rubidium and cesium enter the solution. Lithium is converted into lithium carbonate, and lithium carbonate solid is obtained after ...
Embodiment 2
[0029] Will Li 2 Lepidolite, calcium chloride, sodium hydroxide and composite binder with an O content of 3.1% are mixed in a mass ratio of 1:0.5:0.03:0.3 to produce green pellets of 5-12 mm in size, wherein the composite binder is A mixture of sodium humate, quicklime, sodium carbonate, and potassium carbonate. The above-mentioned green pellets were roasted at 1400°C for 0.5 hours in a "return" shaped orbital roaster, and collected after the furnace gas was cooled to obtain lithium chloride, potassium chloride, sodium chloride, rubidium chloride and cesium chloride Mixture of fumes. Use a solution containing sodium carbonate and potassium carbonate to leach the above-mentioned dust. The content of sodium carbonate and potassium carbonate is greater than 120% of the theoretical amount required to convert lithium in the dust into lithium carbonate. Potassium, sodium, rubidium and cesium enter the solution, and the lithium is converted It is lithium carbonate, and lithium carb...
Embodiment 3
[0033] Will Li 2 Lepidolite, calcium chloride, sodium hydroxide and composite binder with an O content of 4.9% are mixed in a mass ratio of 1:1:0.05:0.1 to produce green pellets of 5-12 mm in size, wherein the composite binder is A mixture of sodium humate, quicklime, sodium carbonate, and potassium carbonate. The above-mentioned green pellets were roasted at 1300°C for 5 hours in a "return" shaped orbital roaster, and collected after the furnace gas was cooled to obtain lithium chloride, potassium chloride, sodium chloride, rubidium chloride and cesium chloride Mixture of fumes. Use a solution containing sodium carbonate and potassium carbonate to leach the above-mentioned dust. The content of sodium carbonate and potassium carbonate is greater than 120% of the theoretical amount required to convert lithium in the dust into lithium carbonate. Potassium, sodium, rubidium and cesium enter the solution, and the lithium is converted It is lithium carbonate, and lithium carbonat...
PUM
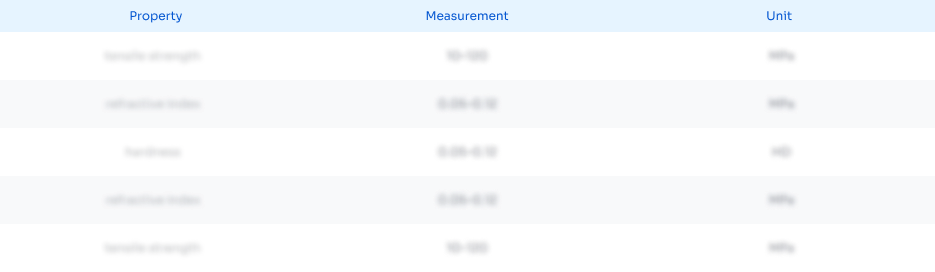
Abstract
Description
Claims
Application Information

- R&D
- Intellectual Property
- Life Sciences
- Materials
- Tech Scout
- Unparalleled Data Quality
- Higher Quality Content
- 60% Fewer Hallucinations
Browse by: Latest US Patents, China's latest patents, Technical Efficacy Thesaurus, Application Domain, Technology Topic, Popular Technical Reports.
© 2025 PatSnap. All rights reserved.Legal|Privacy policy|Modern Slavery Act Transparency Statement|Sitemap|About US| Contact US: help@patsnap.com