Immersed type ultrasonic surface treatment method for polymer 3D printed product
A 3D printing and ultrasonic technology, which is applied in the field of surface processing of polymer 3D printing products, can solve the problems of difficult automation and mass production, difficulty in mastering the accuracy of sandpaper grinding, and processing failure, and achieves easy mass and automated production. , Great application prospects and market value, the effect of high grinding precision
- Summary
- Abstract
- Description
- Claims
- Application Information
AI Technical Summary
Problems solved by technology
Method used
Image
Examples
Embodiment Construction
[0009] Specific embodiments of the present invention will be described in detail below in conjunction with technical solutions and accompanying drawings.
[0010] Step 1: The grinding fluid (5) is configured according to the base material of the product (3) to be processed and the roughness of the surface, and the selection of the particle size of the abrasive particles in the grinding fluid (5) is related to the roughness of the surface of the product. Add the prepared grinding fluid (5) into the grinding pool (1) in the ultrasonic grinding equipment, start the temperature control module (4), and heat to the set temperature;
[0011] Step 2: According to the shape characteristics of the product to be processed (3), select an appropriate clamping bracket (6), so that the product to be processed can be immersed in the grinding fluid (5) without contact with the bottom surface of the grinding pool (1) Or contact with the side wall, multiple OEM products can be clamped on the bra...
PUM
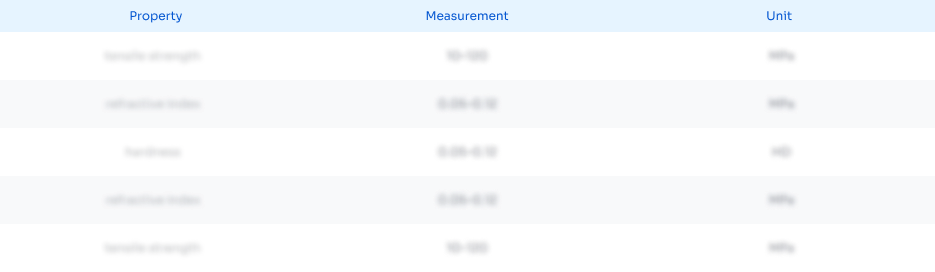
Abstract
Description
Claims
Application Information

- R&D
- Intellectual Property
- Life Sciences
- Materials
- Tech Scout
- Unparalleled Data Quality
- Higher Quality Content
- 60% Fewer Hallucinations
Browse by: Latest US Patents, China's latest patents, Technical Efficacy Thesaurus, Application Domain, Technology Topic, Popular Technical Reports.
© 2025 PatSnap. All rights reserved.Legal|Privacy policy|Modern Slavery Act Transparency Statement|Sitemap|About US| Contact US: help@patsnap.com