Treatment technology of anti-ash-deposition and anti-wear alloy material of waste heat recovery pipeline
A waste heat recovery and alloy material technology, applied in pressure inorganic powder coating and other directions, can solve problems such as increasing failure rate, increasing production cost, wasting dust accumulation, etc., to improve wear resistance and corrosion resistance, increase service life, Avoid the effect of dust accumulation and splashing
- Summary
- Abstract
- Description
- Claims
- Application Information
AI Technical Summary
Problems solved by technology
Method used
Examples
Embodiment 1
[0020] This embodiment provides a treatment process for waste heat recovery pipe alloy materials that are resistant to fouling and wear, including the following specific steps:
[0021] Melting: select the alloy billet, adopt vacuum arc remelting or electroslag remelting, the melting temperature is 3050-3100°C, the chemical composition and mass percentage of the alloy billet are: Al: 11.3%, Mg: 14.6%, Fe: 1.25%, Si : 0.40%, Cu: 0.01%, Mn: 1.5%, Zn: 1.4%, Zr: 0.10%, rare earth element 1.10%, impurity content < 0.015%, and the balance is Ti; among the rare earth, the following components are included by weight percentage : Gd: 15%, Pr: 3%, Dy: 7%, Ac: 12.5%, Nd: 15%, Sm: 11%, and the balance is La;
[0022] Forging: heat the poured steel ingot, the heating temperature is ≤1180°C, the holding time is 2h / 100mm, do not let the flame directly hit the forging;
[0023] Before forging, put the heated scrap steel on the anvil to preheat, put the tongs (or fork) on the furnace door to ...
Embodiment 2
[0029] This embodiment provides a treatment process for waste heat recovery pipe alloy materials that are resistant to fouling and wear, including the following specific steps:
[0030]Melting: select the alloy billet, adopt vacuum arc remelting or electroslag remelting, the melting temperature is 3050-3100 ℃, the chemical composition and mass percentage of the alloy billet are: Al: 12.4%, Mg: 15.5%, Fe: 1.42%, Si : 0.49%, Cu: 0.07%, Mn: 1.6%, Zn: 1.8%, Zr: 0.17%, rare earth element 1.72%, impurity content < 0.015%, and the balance is Ti; among the rare earth, the following components are included by weight percentage : Gd: 16%, Pr: 4%, Dy: 8%, Ac: 12.7%, Nd: 18%, Sm: 12%, and the balance is La;
[0031] Forging: heat the poured steel ingot, the heating temperature is ≤1180°C, the holding time is 2h / 100mm, do not let the flame directly hit the forging;
[0032] Before forging, put the heated scrap steel on the anvil to preheat, put the tongs (or fork) on the furnace door to p...
PUM
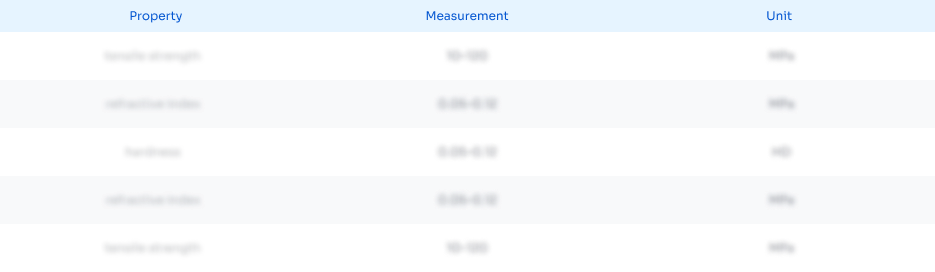
Abstract
Description
Claims
Application Information

- R&D Engineer
- R&D Manager
- IP Professional
- Industry Leading Data Capabilities
- Powerful AI technology
- Patent DNA Extraction
Browse by: Latest US Patents, China's latest patents, Technical Efficacy Thesaurus, Application Domain, Technology Topic, Popular Technical Reports.
© 2024 PatSnap. All rights reserved.Legal|Privacy policy|Modern Slavery Act Transparency Statement|Sitemap|About US| Contact US: help@patsnap.com