Preparation method and application method of hydrated calcium silicate seed crystal
A technology of hydrated calcium silicate and crystal seeds, applied in the direction of silicate, alkaline earth metal silicate, etc., can solve the problem that calcium silicate hydrate seeds are easy to agglomerate, and it is difficult to promote cement hydration and early strength. Not ideal, etc., to achieve good application prospects, excellent early strength effect, and stable product performance.
- Summary
- Abstract
- Description
- Claims
- Application Information
AI Technical Summary
Problems solved by technology
Method used
Image
Examples
Embodiment 1
[0025] Embodiment 1, a kind of preparation method of calcium silicate hydrate seed crystal, take calcium oxide, diatomite, deionized water and dispersant as raw material, calcium silicon ratio is 0.5, water-solid ratio is 1, and dispersant dosage is 0.1%, the reaction temperature is 50°C, the reaction pressure is 0.9MPa, and the reaction time is 10h. The mass ratios of the raw materials are respectively: 100 for calcium oxide, 258 for diatomite, 358 for deionized water, and 0.89 for the dispersant. Prepare according to the steps described in the summary of the invention to obtain the product (denoted as C-S-H-1). Fully mix the slag cement and C-S-H-1 according to the mass ratio of 100:1, and use the water-binder ratio of 0.35 to prepare the clean slurry. The performance test results are shown in Table 1.
Embodiment 2
[0026] Example 2, a method for preparing calcium silicate hydrate seed crystals, using calcium oxide, diatomaceous earth and deionized water as raw materials, the calcium-silicon ratio is 1.2, the water-solid ratio is 10, and the amount of dispersant is 0.3%. The reaction temperature is 120° C., the reaction pressure is 0.3 MPa, and the reaction time is 6 hours. The mass ratio of each raw material is respectively: 100 for calcium oxide, 108 for sodium silicate, 2080 for deionized water, and 1.56 for dispersant. Prepare according to the steps described in the summary of the invention to obtain the product (denoted as C-S-H-2). Fully mix the slag cement and C-S-H-2 according to the mass ratio of 100:2, and prepare the clean slurry with the water-binder ratio of 0.35. The performance test results are shown in Table 1.
Embodiment 3
[0027] Example 3, a method for preparing calcium silicate hydrate seed crystals, using calcium oxide, sodium silicate and deionized water as raw materials, the calcium-silicon ratio is 2.5, the water-solid ratio is 20, and the amount of dispersant is 0.5%. The reaction temperature is 180° C., the reaction pressure is 0.1 MPa, and the reaction time is 2 hours. The mass ratio of each raw material is respectively: 100 for calcium oxide, 204 for sodium silicate, 6080 for deionized water, and 3.8 for dispersant. Prepare according to the steps described in the summary of the invention to obtain the product (denoted as C-S-H-3). Fully mix the slag cement and C-S-H-3 according to the mass ratio of 100:5, and use the water-binder ratio of 0.35 to prepare the clean slurry. The performance test results are shown in Table 1.
[0028] Table 1 embodiment performance test result
[0029]
PUM
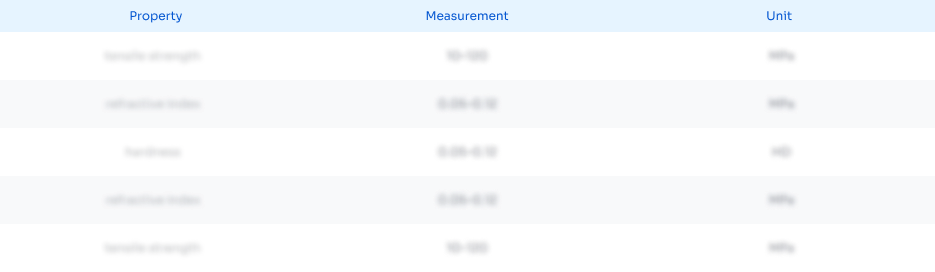
Abstract
Description
Claims
Application Information

- R&D
- Intellectual Property
- Life Sciences
- Materials
- Tech Scout
- Unparalleled Data Quality
- Higher Quality Content
- 60% Fewer Hallucinations
Browse by: Latest US Patents, China's latest patents, Technical Efficacy Thesaurus, Application Domain, Technology Topic, Popular Technical Reports.
© 2025 PatSnap. All rights reserved.Legal|Privacy policy|Modern Slavery Act Transparency Statement|Sitemap|About US| Contact US: help@patsnap.com